Refractory plastics are made of 70~80% granular and powdery materials, 10~25% plastic clay, and other binders and appropriate plasticizers. They are in the form of hard mud paste and maintain high plasticity for a long time. Refractory plastics are mainly used in various heating furnaces that are not in direct contact with the melt. The materials are mostly clay and high alumina, but also silicon, magnesium, chromium, zircon, and silicon carbide. If classified by binder, there are clay-bonded, water glass-bonded, phosphate-bonded, sulfate-bonded plastics, etc.
Rongsheng Refractory Plastic Manufacturer
The aggregates used in refractory plastics mainly include special-grade clay clinker, third-grade, second-grade, or first-grade alumina clinker, etc. The maximum particle size of refractory aggregate is 10mm, and its particle grading is: 10~5mm, 33%~40%. 5~3mm, 28%~35%. Less than 3mm, 28%~35%. It should be pointed out that 0.5~0.09mm particles should be minimized or eliminated. The amount of aggregate is 55%~65%.
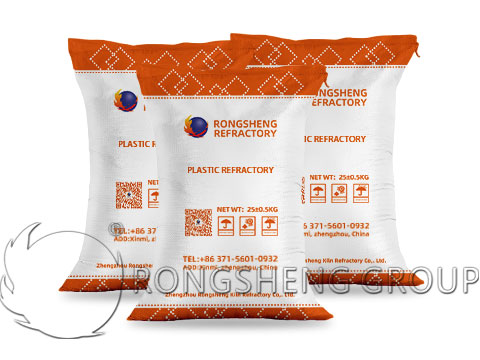
Refractory powder is generally made of special-grade, first-grade or second-grade alumina clinker, and its fineness of ≤0.09mm should account for 95%. In fact, the finer the better. It is strictly forbidden to use underburned materials or clay clinker as refractory powder. The amount of refractory powder is 20%~30%.
In order to ensure smooth construction and normal use at high temperatures, refractory plastics should generally have the following basic properties:
- ① Have a certain degree of plasticity to facilitate construction.
- ② Have a certain shelf life to ensure that the molding performance remains unchanged during the specified storage period.
- ③ Have a certain strength after room temperature curing to facilitate the removal of the frame or transportation after construction.
- ④ Have a certain high-temperature volume stability to prevent damage to the furnace lining structure due to excessive deformation.
Common Bonding Methods for Wear-Resistant Refractory Plastics
Wear-resistant and fire-resistant plastics are made of 70%-85% granular and powdery materials, 10%-20% plastic clay, and other binders and appropriate plasticizers. Some air-hardening and heat-hardening binders and admixtures are also added to improve performance. Plastics can be divided into clay bonding, water glass bonding, phosphoric acid bonding, aluminum sulfate bonding, tar-asphalt, composite bonding, or resin bonding according to the binder.
- Clay bonding: Raw clay is the main binder. Clay plays a plasticizing and bonding role in plastics, which can bond refractory aggregates and powder together, giving plastics good plasticity and facilitating construction. However, there are many impurities in clay, and excessive addition will reduce the hot strength and corrosion resistance of plastics.
- Phosphoric acid and phosphate bonding: Phosphoric acid and phosphate solutions as binders can improve the performance of plastics, especially at high temperatures, which can make plastics obtain higher strength and have good wear resistance and corrosion resistance. However, phosphoric acid and phosphates easily react chemically with refractory powder and raw clay, causing the plastic to lose its plasticity, so inhibitors are usually required.
- Aluminum sulfate bonding: Aluminum sulfate solution is often used as a binder, which can improve the strength and stability of plastics to a certain extent. It has a relatively low cost and a wide source. Its bonding effect is good, which can make the plastic have a certain strength at room temperature and facilitate construction operations.
- Water glass bonding: Water glass solution as a binder can enhance the gas hardness of plastics and has a low cost. However, the Na₂O brought in by water glass will reduce the refractory performance, and it is easy to form a film on the surface during the drying process, which affects the removal of moisture and is not conducive to the drying of the lining.
- Tar-asphalt or resin bonding: In some special occasions, tar-asphalt or resin will be used as a binder. This type of binder can give plastics better slag resistance and corrosion resistance, and can form a certain carbon skeleton at high temperature to improve the strength and stability of plastics.
- Composite bonding: using two or more binders to work together, such as a composite bonding method of hydration bonding and coagulation bonding, which combines the advantages of multiple binders. It can make the plastic have good toughness, thermal shock stability, volume stability, and other comprehensive properties.