In the monolithic refractories, the proportion of aggregate and powder is relatively large, while the proportion of binder and other components is relatively low. Unshaped refractories are mainly composed of some aggregates and powders. Because the refractory ramming material is mainly used in the place where it is in direct contact with the melt, the aggregate and powder are required to have high volume stability, compactness, and corrosion resistance. Raw materials for refractory ramming mix materials are usually sintered or melted materials at high temperatures. The carbon refractory ramming material manufacturer for blast furnaces, Rongsheng refractory material manufacturer, has an environmentally friendly and advanced automatic monolithic refractory production line, as well as professional monolithic refractory technicians. Specializing in providing solutions for refractory lining material configuration for various kiln refractory linings.
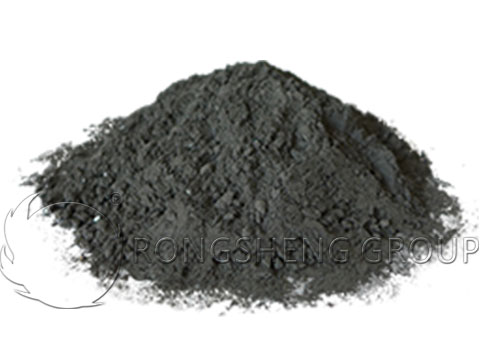
For refractory ramming materials, the appropriate binder is usually selected according to the materials of aggregates and powders, as well as application requirements. Ramming mass materials are commonly used as binders such as water glass, silica gel, ethyl silicate, and refractory clay. The dry ramming material uses boric acid. Brine, phosphate, magnesium sulfate, coal tar, etc. are commonly used as binders for basic ramming materials. Some ramming mix materials require no binder, or only a small amount of iron oxide powder (such as iron oxide powder) is added to make it sintered.
The Blast Furnace Adopts Carbon Refractory Ramming Mix Material
The carbon refractory ramming mix material for the blast furnace is mainly used to fill the gap between the carbon brick and the cooling wall, and the gap between the carbon brick at the bottom of the furnace and the sealing plate at the bottom of the furnace. The mashed carbon material should have a certain strength and density. The role of carbon refractory ramming material used in the blast furnace is as follows.
- ①Efficient heat transfer. If the thermal conductivity of carbon refractory ramming mix material is too low, it will affect the smooth transfer of furnace heat. It is possible to increase the temperature of the carbon bricks and accelerate the corrosion of the furnace.
- ② Carbon refractory ramming mix material can play the role of the refractory brick lining. In the later stage of the blast furnace, if the carbon bricks are in danger of burning through or iron infiltration, the carbon ramming material layer can also partially play the role of carbon bricks.
- ③ Hearth carbon ramming material has the function of caulking. At the same time, it also plays the role of absorbing the expansion stress generated by the lining of carbon bricks and other refractory bricks during the heating process. In order to prevent the furnace shell from cracking due to excessive force.
At present, the thermal conductivity of microporous carbon bricks in China has reached about 20W/(m·K). In order to transfer heat efficiently, the thermal conductivity of the ramming mix material should match it. Otherwise, a thermal resistance layer will be formed, which will affect the smooth release of heat. Therefore, the development direction of carbon refractory ramming mix material is as follows.
- ①Construction at room temperature can be achieved.
- ②Has good molding performance and construction performance.
- ③The thermal conductivity is measured at 120℃.
- ④The thermal conductivity matches the thermal conductivity of the selected carbon bricks.
The blast furnace adopts carbon refractory ramming material, and the crushed material is granular. According to the needs of uses, a variety of materials can be used to make powder. Regardless of the material used, the ramming mass is mainly used for direct contact with the molten material. Granular powders are required to have high volume stability, compactness, and corrosion resistance. High-temperature sintered or melted materials are generally used. Those used on inductive lines should also be insulated.