Dry ramming materials can be constructed by direct vibration or direct vibration. The direct ramming method is to use a vibrator to directly ram the refractory material. After fully vibrating a layer of refractory material with a rammer, rake its surface, then fill it with a new layer of material, and then fully vibrate it with a rammer. This is done layer by layer until the construction is completed. Although this method is time-consuming, it can prevent delamination between layers. Direct vibration is the vibration force generated by the ramming device fixed on the inner or outer mold, and then transmitted to the refractory material through the template, thereby densifying the ramming material.
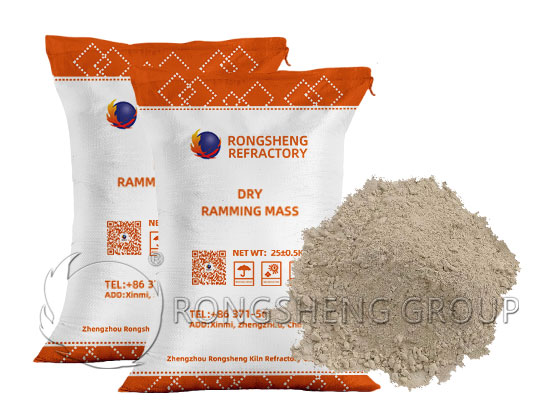
Refractory Ramming Material for Electric Furnace Bottom
In terms of the selection of refractory materials for the working layer at the bottom of the electric furnace, magnesia dry ramming materials are now widely used in the working layer of high-power and ultra-high-power electric furnaces. Since the refractory material used in the furnace bottom working layer is in direct contact with molten steel and slag. Directly withstand high-temperature heat load and corrosion of slag, erosion of molten steel, mechanical impact of scrap steel, and oxidation and recovery operations at high temperatures in the furnace, causing the slag to penetrate into the furnace bottom, causing the furnace bottom to become thinner. During discontinuous operation, the dicalcium silicate in the slag absorbs moisture in the atmosphere and collapses. Reduce the durability of the material and affect its service life. Therefore, this layer of refractory material should have strong sintering ability, rapid sintering at a guaranteed sintering temperature, and the formation of a sintered layer with a certain strength and thickness, which is enough to withstand the mechanical impact of the charge.
Filling Density in Dry Ramming Material Construction
The filling density of the dry ramming material after molding is closely related to the pre-pressure and vibration force of the vibrator, the vibration frequency and the number of vibrators. Preloading can improve the initial filling density. Increasing the vibration frequency can also increase the filling density. When the ramming frequency is above 50Hz, increasing the vibration force can effectively increase the filling density of the vibrating body. When the dry vibrating material is not pre-pressed, the vibration force generated by two mutually perpendicular rammers can also achieve a sufficiently fine effect.
The material is composed of high-iron and high-calcium magnesia and electrolytic magnesia as aggregates. Composed magnesia and fused magnesia are used as fine powder, and the critical particle size is 5-6mm. C2F (dicalcium ferrite) in the magnesia composition is used as a sintering aid. No binding agent is added, and it is made of multi-stage ingredients. Through strong ramming construction, the density after construction is ensured, and it can be sintered into a solid whole at the appropriate temperature. Its service life is several times longer than the previous knotting and bricklaying methods.
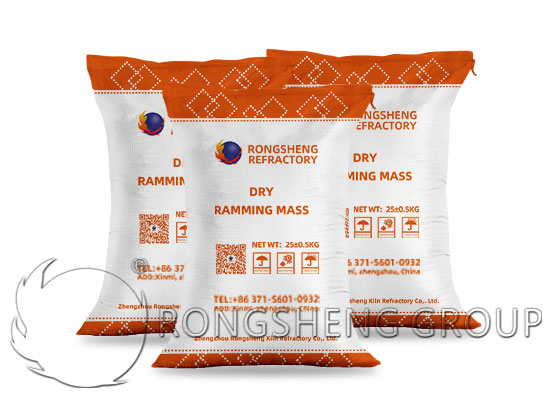
Construction and Drying of Medium Frequency Electric Furnace Dry Ramming Materials
Correct furnace building, baking, and sintering processes are the key to ensuring the normal operation of the furnace lining.
Before dry-tying the furnace lining, first lay a layer of asbestos board and a layer of glass fiber cloth inside the insulation layer of the furnace coil. During laying, in addition to manually smoothing and compacting each layer of materials, spring coils are also used to tighten them up and down. When tamping the quartz sand, move the spring rings one by one from top to bottom until the furnace lining is knotted.
Knot the hearth bottom. The furnace bottom is about 280mm thick and is filled with sand in four stages. When manually knotting, prevent uneven density everywhere and non-density of the furnace lining after baking and sintering. Therefore, the feeding thickness must be strictly controlled. Generally, the sand filling thickness is no more than 100mm per time, and the furnace wall is controlled within 60mm. Multiple people operate in shifts, with 4-6 people per shift, and each knotting takes 30 minutes to change people. Rotate slowly around the stove and apply even pressure to avoid uneven density.
When the knotted bottom of the furnace reaches the required height, it is scraped off and the crucible mold can be placed. In this regard, care should be taken to ensure that the crucible mold and the induction coil are concentric and the vertical adjustment is made up and down. The shape should be as closely integrated with the furnace bottom as possible. After adjusting the surrounding gaps to be equal, use three wooden wedges to tighten them. A heavy object is placed in the middle to prevent the quartz sand from shifting when the furnace wall is knotted.
Knotted hearth wall. The furnace lining thickness is 110-120mm. Add the dry ramming material in batches, spread it evenly, and the thickness of the filler should not be greater than 60 mm. Knot it for 15 minutes (manual knotting) until it is flush with the upper edge of the induction coil. The crucible mold is not taken out after the knotting is completed, and it functions as induction heating during drying and sintering.
Baking and sintering specifications. To obtain the three-layer structure of the furnace lining, the baking and sintering process is roughly divided into three stages.
- Baking stage. Heat the crucible mold to 600°C at a rate of 25°C/h and 50°C/h respectively, and keep it warm for 4 hours. The purpose is to completely remove moisture from the furnace lining.
- Semi-sintered stage. Raise the temperature to 900°C at 50°C/h and keep warm for 3 hours. Raise the temperature to 1200°C at 100°C/h and keep it warm for 3 hours. The heating rate must be controlled to prevent cracks.
- The Complete sintering stage. When sintering at high temperatures, the sintered structure of the crucible is the basis for improving its service life. If the sintering temperature is different, the thickness of the sintering layer is insufficient, and the service life is significantly reduced.
The 2T intermediate frequency furnace adds about 950 kilograms of iron material during the baking process to enhance the heating effect of the induction coil. As baking and sintering continue, a relatively stable electromagnetic force is generated through low-power power transmission to stir the molten iron, so that the top and bottom of the furnace lining are heated evenly. Strictly control the temperature of the three phase change zones of quartz sand to promote sufficient phase change of quartz sand. The first sintering strength of the furnace lining is improved.
Regarding the life of the intermediate frequency furnace lining, in addition to ensuring a complete and reasonable three-layer lining, attention should also be paid to daily operations. To build a furnace, high-quality and clean furnace-building materials are selected, reasonably proportioned, and carefully knotted. Scientific baking and sintering specifications and strict operating techniques can extend the service life of the furnace.

Rongsheng Monolithic Refractory Materials Manufacturer
Rongsheng Unshaped Refractory Materials Manufacturer is a refractory material manufacturer with rich production and sales experience. Our environmentally friendly, fully automatic unshaped refractory material production line provides a reliable guarantee for the long life and efficient use of the overall refractory lining of high-temperature industrial furnaces. Our professional technical team can customize refractory lining solutions based on the actual working conditions of high-temperature industrial furnaces. At the same time, our comprehensive customer service also relieves many customers from worries. We have won continuous return orders from many customers. Contact us to get a free refractory lining solution and quote.