At present, the working layer of high-power and ultra-high-power electric furnaces is generally constructed with magnesia dry ramming material. The refractory materials used in the working layer are in direct contact with molten steel and slag. Directly withstand high-temperature heat load and erosion of molten slag, erosion of molten steel, mechanical impact of scrap steel, and oxidation and reduction operations at high temperatures in the furnace, causing molten slag to penetrate into the furnace bottom, causing the furnace bottom to become thinner. During discontinuous operation, the dicalcium silicate in the slag absorbs moisture in the atmosphere and falls off, reducing the durability of the material and affecting its service life.
Common dry ramming materials use high-iron and high-calcium synthetic magnesia and fused magnesia as aggregates. Synthetic magnesia and fused magnesia are used as fine powder, and the critical particle size is 5~6mm. It uses C2F (dicalcium ferrite) in synthetic magnesia as a sintering aid, without adding any binding agent, and is made of multi-stage ingredients. Through strong ramming construction, the density after construction is ensured, and it can be sintered into a solid whole at an appropriate temperature. Its lifespan is several times longer than the previous knotting and bricklaying methods. The dry ramming materials used in intermediate frequency furnaces have higher quality requirements. Some scholars have studied the use of fused corundum, white corundum, tabular corundum, and magnesia as granular materials, and magnesia fine powder and corundum fine powder as powder. Add high-temperature burning accelerator and boric acid as admixture. Mix various raw materials evenly and adjust the particle gradation to make dry ramming material.
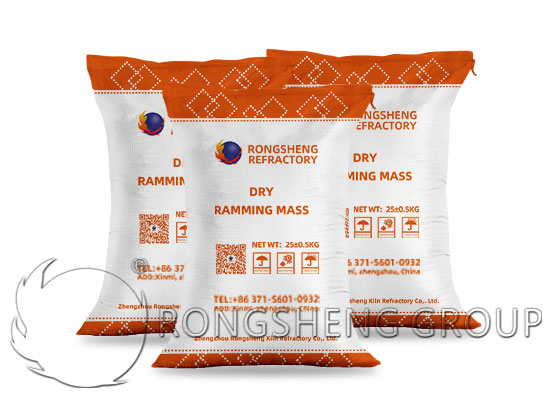
Before construction of electric furnace bottom dry ramming material, attention should be paid to cleaning up the permanent layer residue, dust, iron wire, plastic sheet and other foreign matter. Calculate the knot size. The actual knot thickness is equal to the required knot thickness multiplied by 1.09. And prepare a sufficient amount of ramming material according to the construction furnace slope and furnace bottom size requirements. After the materials are received, check whether there are any debris or moisture in the ramming materials. The debris should be cleaned up, and the damp materials should not be used. And prepare knotting equipment such as tamping machine, pneumatic pick, etc.
Construction of Dry Ramming Material at the Bottom of Electric Furnace
For the specific construction steps of dry ramming material at the bottom of electric furnace, please refer to the following plan:
Use a shovel to spread the material flat, and then step firmly with your feet to remove the air. After firming, insert the steel drill into the material and shake it repeatedly, then use your feet to firm it further. The appropriate construction thickness of each layer of ramming material is 150~200mm. Then use a knotting tool to repeatedly pound the knot 3 times in a spiral shape from the periphery to the center.
The method to check the knotting quality is usually to place a round steel with a diameter of 5mm on the ramming layer and press it down with a pressure of 10kg, so that its depth does not exceed 30mm. During on-site construction, a steel drill can be used to insert it forcefully, and its depth should not exceed 30mm.
The method of knotting the furnace slope is the same as that of the furnace bottom. First, use your feet to firmly hit it, and then use a knotting tool to pound it. The maximum angle between the furnace slope and the furnace bottom shall not exceed 40°. Prevent material from rolling or collapsing due to excessive furnace slope.
In places where the molten steel is agitated and eroded severely, such as the tapping seat brick and the furnace door, it should be pounded vigorously and the size can be appropriately thickened. In order to extend the service life of the refractory materials in these damaged parts as much as possible.
After the ramming is completed, cover the ramming material with a 5~10mm thick steel plate to prevent the shape of the furnace bottom from being damaged when loading scrap steel or the scrap steel being inserted into the ramming material layer, causing hidden dangers of steel leakage. If steel cannot be made in time, add 100~200mm thick lime on the iron plate to prevent hydration of the ramming material.
When knotting the ramming material, you must strictly follow the construction requirements to ensure the density of the ramming material. Otherwise, the ramming material will shrink severely during use, causing a large number of cracks to cause peeling, resulting in a reduction in service life. The first furnace smelting is very important. When blowing oxygen for decarburization, the oxygen blowing pipe must not be inserted too deep, otherwise it will easily cause the ramming material at the bottom of the furnace to turn up and create a big pit. During the first furnace smelting, a layer of lime can be laid on the bottom of the furnace to prevent scrap steel from directly hitting the bottom of the furnace. It also prevents hydration of the ramming material and early formation of slag.
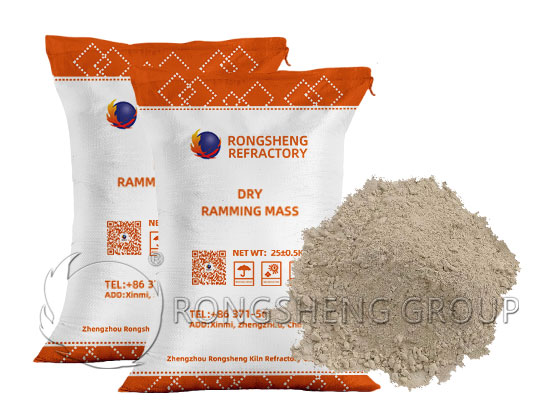
Periodic Repair of Dry Ramming Materials
Under normal circumstances, the one-time service life of dry ramming materials can reach more than 300 furnaces. Through hot repair, the service life can be extended to 500~600 furnaces, and some products on the market can even reach more than 600 furnaces.
After the electric furnace bottom ramming material is used for a certain period of time, due to various reasons, the electric furnace bottom will be damaged to varying degrees. Therefore, the furnace lining should be repaired according to the damage to the furnace lining.
- (1) Hot repair is performed at certain intervals during smelting. However, after each furnace of steel is produced, close attention must be paid to the dynamics of the furnace bottom. If a pit with a depth greater than 150mm is found, it must be repaired.
- (2) Blow the repaired surface with oxygen before repairing to completely remove the remaining steel residue in this area. Note that it needs to be done immediately after steel and slag are removed.
- (3) Hoist the ramming material until it falls above the area to be repaired, and move the crane to make it reasonably distributed.
- (4) Lift in iron blocks or other heavy objects and compact them.
- (5) It needs to be emphasized that if a large area of the furnace bottom and furnace slope is hot repaired, in order to ensure the service life after repair, the number of repairs should be shortened and the consumption of tons of steel for dry ramming materials should be reduced. The first furnace steel after hot repair can be smelted according to the “New Furnace Smelting Operation Requirements”.

Problems and Maintenance During the Use of Dry Ramming Furnace Bottom Lining
During the use of dry ramming materials, the following problems are prone to occur.
- Cold repair the bottom of the furnace to turn up in lumps.
For the cold repaired furnace bottom, when it is used for a certain number of times, sometimes a certain part will turn up in a lump. In order to prevent this phenomenon from happening, the thickness of the cold repair layer should be ensured to be no less than 150mm, and the residue at the bottom of the original furnace should be cleaned strictly as required. When the thickness of the cold repair layer is thin, attention should be paid to adding light materials first to avoid heavy mechanical impact on it and causing it to float after being broken. In terms of dry ramming materials, the Fe2O3 content in the materials can be appropriately increased to facilitate the sintering bond between the cold repair layer and the original furnace bottom.
- A powdery layer appears at the bottom of the dry ramming material furnace.
When a furnace service is completed and cooled, the working layer at the bottom of the dry ramming material furnace will produce a pulverized layer of about 30mm. The formation of a powdery layer on the surface does not affect the normal use of dry ramming materials, but it will cause additional consumption of materials and increase production costs. For this reason, the composition of the material can be changed so that the dry ramming material contains more Fe2O3 and appropriate CaO to reduce or eliminate the slag infiltration and powdery layer.
- Steel infiltration of the sintering layer at the furnace bottom.
After a furnace service, the sintered layer at the bottom of the furnace has steel penetration. When cleaning the remaining steel and residue, the sintered layer will be pulled up together, causing additional consumption of materials. Therefore, the molten steel should be drained out as much as possible before shutting down the furnace. After the furnace is shut down, measures should be taken, such as covering the furnace bottom with steel plates, to reduce the cooling rate of the furnace bottom and prevent or reduce thermal shock shrinkage cracks. In addition, the properties of the material itself should be improved to prevent excessive sintering shrinkage and prevent sintering shrinkage cracks.
- The dry ramming material furnace bottom erodes too quickly.
The bottom of a dry ramming material furnace sometimes suffers from corrosion soon after being used. This is mainly due to quality problems in the material, resulting in poor sintering of the material, poor high-temperature performance of the binding phase, and high liquid content inside the material at high temperatures. Good raw materials can be selected to reduce the amount of liquid phase produced by dry ramming materials at high temperatures. In addition, the material composition should be adjusted. An appropriate amount of Fe2O3 content (Fe2O3 content is controlled between 4.0% and 6.0%) and a sintering agent are the keys to improving the sintering properties of the material.