Refractory monolithics play a crucial role in high-temperature industrial applications, providing insulation, protection, and durability. Proper installation and maintenance of these materials are essential for ensuring their longevity and optimal performance. From RS Monolithic Refractory Factory, we know the importance of proper installation and maintenance of refractory monolithics and how they can impact industrial processes.


Proper Installation of Refractory Monolithics
Proper installation of refractory monolithics involves several critical steps. The first step is to choose the right type of material based on the specific application requirements. The material selected should have appropriate physical properties, such as thermal conductivity, thermal expansion, and strength, to withstand the high-temperature environment. The installation process should also take into account the shape and size of the surface to be coated, as well as any design considerations such as expansion joints or anchors.
Once the appropriate material has been selected, the surface to be coated should be thoroughly cleaned and prepared to ensure good adhesion. This may involve removing any existing coatings or debris and roughening the surface to improve adhesion. The monolithic refractory material is then mixed according to the manufacturer’s instructions and applied to the surface in layers. It is important to ensure that each layer is allowed to dry and cure properly before the next layer is applied.
Maintenance of Refractory Monolithics
After installation, proper maintenance of refractory monolithics is essential to ensure their longevity and optimal performance. Regular inspections should be performed to detect any signs of damage or wear, such as cracking, spalling, or erosion. Any areas of damage should be repaired promptly to prevent further deterioration and ensure continued protection of the underlying substrate.
In addition to visual inspections, regular testing of the material’s physical properties, such as thermal conductivity and strength, should be conducted to monitor its performance over time. Any changes in these properties may indicate a need for maintenance or replacement.
Proper maintenance of refractory monolithics also includes taking steps to prevent damage from factors such as thermal shock, chemical attack, or mechanical stress. This may involve controlling the rate of temperature change, using protective coatings or barriers, or avoiding exposure to corrosive substances.
Failure to properly install and maintain refractory monolithics can have serious consequences for industrial processes. Damage or wear to these materials can lead to reduced insulation, decreased durability, and increased heat loss. This can result in decreased efficiency, increased energy costs, and even process failures or safety hazards.
In conclusion, proper installation and maintenance of refractory monolithics are essential for ensuring their longevity and optimal performance in high-temperature industrial applications. Choosing the right material, following proper installation procedures, and conducting regular inspections and testing can help prevent damage and ensure continued protection and efficiency. By investing in proper installation and maintenance of refractory monolithics, industrial processes can avoid costly downtime and ensure safe and reliable operations.
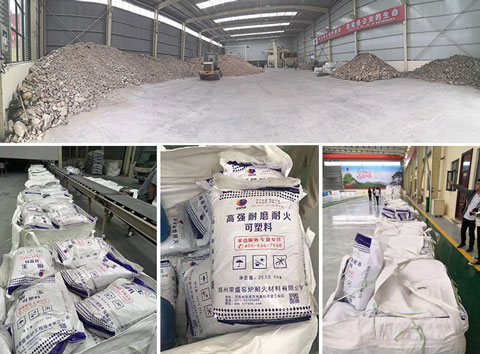
The Advantages of Using Refractory Monolithics in High-Temperature Applications
Refractory monolithics are essential materials in high-temperature applications due to their ability to withstand extreme heat, chemical corrosion, and mechanical stress. These materials have several advantages over traditional refractory materials such as bricks or castables, making them an increasingly popular choice for industrial processes. In this blog post, we will explore the advantages of using refractory monolithics in high-temperature applications.
One of the main advantages of refractory monolithics is their ability to provide a more precise and uniform lining than traditional refractory materials. Monolithics are cast in place, allowing for custom shapes and sizes to be created to fit the specific application requirements. This ensures a perfect fit and eliminates the need for additional cutting or shaping of the material, reducing both installation time and costs.
Refractory monolithics are also known for their high thermal shock resistance, which is the ability to withstand rapid temperature changes without cracking or spalling. This property makes them particularly useful in applications where rapid heating and cooling cycles occur, such as in steelmaking, glassmaking, or chemical processing.
Another advantage of refractory monolithics is their high chemical resistance, making them ideal for use in applications where exposure to acids, alkalis, or other corrosive substances is common. Monolithics can be formulated to resist specific chemical environments, ensuring long-lasting protection and reducing the need for frequent replacements.
Refractory monolithics are also known for their excellent insulating properties, providing superior heat retention and energy efficiency compared to traditional refractory materials. This can lead to reduced energy costs and increased productivity, as less energy is needed to maintain high-temperature processes.
Finally, refractory monolithics offer a high degree of flexibility in design and application, making them suitable for a wide range of industrial processes. They can be used in various shapes and sizes, including curved and irregular surfaces, and can be applied using various techniques such as gunning, casting, or ramming.
In conclusion, the advantages of using refractory monolithics in high-temperature applications are numerous, including precise and uniform lining, high thermal shock resistance, excellent chemical resistance, superior insulation, and flexibility in design and application. These properties make them an increasingly popular choice for industrial processes where high temperatures, corrosive environments, and energy efficiency are critical. By using refractory monolithics, industrial processes can ensure long-lasting protection, increased productivity, and reduced costs.