Refractory materials are essential components in industries that require high-temperature processing. They are used in various applications, such as furnaces, kilns, and reactors. Refractory materials must have excellent thermal shock resistance, high mechanical strength, and chemical stability to withstand the extreme conditions of these high-temperature processes. Low cement castables are a type of refractory castable material that offers several advantages over traditional refractory materials in high-temperature applications. High-temperature applications pose a significant challenge to industrial processes. Traditional refractory materials, such as bricks and ceramic fibers, have been widely used to withstand high temperatures. However, these materials have limitations. This is where low cement castables refractory come into play. In this essay, we will discuss the advantages of using low-cement castables in high-temperature applications.

Using Low-Cement Castables in High-Temperature Applications
Low cement castables, also known as LCC, are a type of refractory material that contains a lower percentage of cement content than traditional castables. The lower cement content results in a higher amount of aggregates and additives, providing excellent strength and resistance to abrasion and erosion. Low cement castables refractory are used in applications where high temperatures and harsh conditions are present, such as in the steel, cement, and petrochemical industries.
One significant advantage of low cement castables is their high density and low porosity. This property ensures that they have excellent resistance to thermal shock, abrasion, and chemical corrosion. When used in refractory linings, low-cement castables refractory offer improved insulation and protection against high-temperature processes. They also offer better heat retention, which improves energy efficiency and reduces the amount of fuel required to maintain high temperatures.
Low cement castables also provide improved mechanical strength and durability. They have a lower percentage of cement content than traditional refractory materials, which allows for more aggregate and additives to be added. This results in a denser and stronger refractory lining that is better able to withstand high stresses and pressures. The increased strength and durability of low cement castables refractory make them ideal for use in areas of refractory linings that are subject to heavy wear and tear, such as furnace linings.
Another advantage of low cement castables is their ability to resist chemical corrosion. The lower cement content in these materials means that they are less susceptible to chemical attack and erosion. This makes them ideal for use in the petrochemical industry, where they come into contact with corrosive chemicals and acids.
Low cement castables are also easier to install than traditional refractory materials. They require less water and less curing time, which means that they can be installed more quickly. This reduces downtime and increases productivity, making them a cost-effective solution for refractory linings.

In conclusion, low cement castables offer several advantages over traditional refractory materials in terms of improving the performance of refractory linings. They provide better insulation, heat retention, mechanical strength, and resistance to thermal shock and chemical corrosion. They are also easier to install and cost-effective. Low cement castables refractory are an excellent choice for industries that require high-temperature processing, and their use can improve efficiency, reduce costs, and increase the lifespan of the equipment. As such, they are a valuable addition to any industrial refractory lining application.
The Role of Additives in Enhancing the Properties of Low-Cement Castables
Low cement castables (LCC) are a type of refractory material that offer several advantages over traditional castables. They have a lower percentage of cement content, resulting in a higher amount of aggregates and additives. This composition gives them excellent strength, resistance to abrasion and erosion, and superior thermal shock resistance. However, to further enhance their properties, additives can be used. In this essay, we will explore the role of additives in enhancing the properties of low-cement castables.
Additives are materials that are added to low-cement castables to improve their properties. There are various types of additives, including plasticizers, dispersants, and fibers. Plasticizers are used to improve the workability and flowability of the castable mix. Dispersants are used to improve the homogeneity and distribution of the castable mix. Fibers are added to improve the mechanical strength and resistance to cracking of the castable.
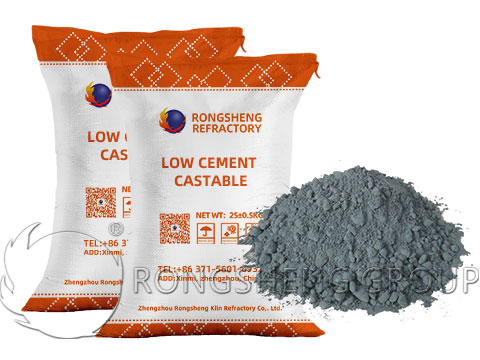
One significant advantage of using additives in low-cement castables is the improvement of their mechanical strength. By adding fibers, such as steel or ceramic fibers, to the mix, the resulting castable has improved tensile and flexural strength. This is particularly important in areas of the refractory lining that are subject to high stress and mechanical wear.
Additives can also improve the thermal shock resistance of low-cement castables. Thermal shock occurs when a refractory material is exposed to rapid changes in temperature, resulting in cracking and damage. By adding certain types of fibers, such as alumina fibers, to the castable mix, the resulting castable can better resist thermal shock.
Another advantage of using additives is the improvement of the castable’s abrasion and erosion resistance. The addition of silicon carbide or other types of hard aggregates can improve the castable’s resistance to abrasion and erosion. This is particularly important in areas of the refractory lining that are subject to high abrasion or where the flow of materials causes erosion.
Additives can also improve the workability and flowability of the castable mix, making it easier to install. This results in less downtime and increased productivity, which is essential in industrial applications.
Additives for Low Cement Castables
Low cement castables (LCC) are a type of refractory material that has gained popularity in high-temperature processing industries due to their superior properties. However, to further enhance their properties, additives are often incorporated into their composition. Additives play a significant role in improving the performance of low-cement castables. In this essay, we will explore the role of additives in enhancing the properties of low-cement castables.
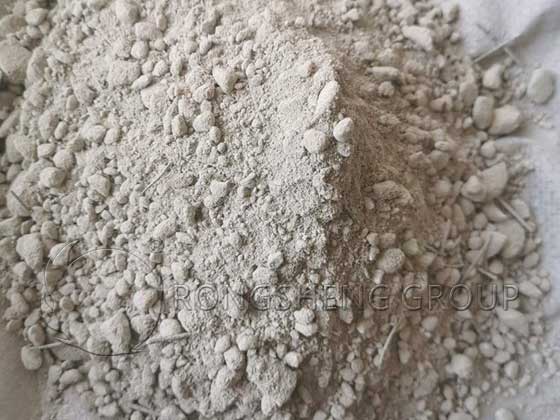
One of the most common additives used in low-cement castables is micro-silica. Microsilica is a fine-grained, amorphous silica powder that can enhance the properties of LCC in several ways. It can improve the flowability of the mix, resulting in better packing density and a more homogeneous cast. Microsilica can also improve the mechanical strength of the LCC, resulting in better resistance to thermal shock and abrasion.
Another common additive used in low-cement castables is alumina. Alumina is added to the mix to increase the refractoriness of the LCC. It also enhances the mechanical properties of the LCC by increasing its strength and toughness. Alumina can also improve the resistance of LCC to thermal shock, which is crucial in high-temperature processing industries.
Zirconia is another additive that is commonly used in low-cement castables. Zirconia is added to the mix to improve the corrosion resistance of the LCC. It is particularly useful in applications where the LCC comes into contact with acidic or basic environments. Zirconia also enhances the mechanical properties of the LCC by improving its strength and toughness.
Other additives that can be used in low-cement castables include calcium aluminate cement, graphite, and metallic fibers. Calcium aluminate cement can improve the setting time of the LCC and enhance its mechanical properties. Graphite can improve the thermal conductivity of the LCC and increase its resistance to thermal shock. Metallic fibers can enhance the mechanical properties of the LCC by providing additional reinforcement.
In conclusion, additives play a critical role in enhancing the properties of low-cement castables refractory. They can improve the flowability, refractoriness, mechanical strength, and resistance to thermal shock and corrosion of the LCC. The use of additives allows for the customization of LCC to suit specific applications, making them an ideal choice for high-temperature processing industries. With the proper selection and incorporation of additives, the performance of low-cement castables can be further enhanced, resulting in more efficient and cost-effective refractory solutions.