Tundish dry ramming mix material. Dry Ramming Material is an unshaped refractory material formed by vibration method without adding water or liquid binder. Under the action of vibration, the material can form a dense and uniform whole. When heated, thermosetting binders or ceramic sintering agents are used to create strength. Dry vibrating materials are composed of refractory aggregates, powders, sintering, and admixtures.
Tundish Dry Ramming Material
The tundish dry ramming material flows easily under the action of vibration force. Among them, the powder can fill the very small pores between the particle accumulations even under the action of a small vibration force, and obtain a dense body with a high filling density. During use, a layer of working surface with a certain strength is formed by heating. However, there are still parts of the non-working surface that are not sintered and show the original dense packing structure. This structure helps to reduce the stress caused by expansion or contraction; helps to hinder the spread and extension of cracks; and helps to prevent the intrusion of metal melt. It makes for easy unpacking and cleaning. This material is applied at the construction site using vibration methods. The construction is simple, the construction period is short, no maintenance and baking are required, and the working layer can be directly sintered and put into use by rapidly heating up the working layer.
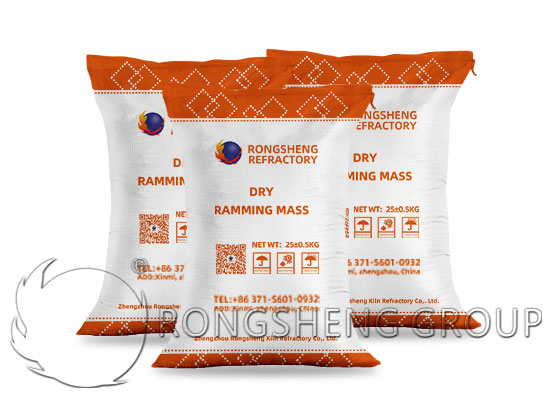
Characteristics of Tundish Dry Ramming Material
- Rapid construction. With the right construction methods the job can be completed in just a few minutes. It greatly reduces the labor intensity of workers and reduces safety hazards caused by human factors.
- Dry molding. It can be put into use without long baking time, which reduces energy consumption. Greatly speeding up the turnover speed of intermediate packages.
- Good corrosion resistance improves the life of the lining. It meets the need for long-term steel pouring and greatly reduces steelmaking costs.
- Rely on phenolic resin as a binding agent to obtain demoulding strength. Reduce phosphorus pollution and purify molten steel. It can meet the requirements of smelting different steels. However, resin-bonded dry ramming mass materials are prone to carbonization.
There are reasonable line changes under various temperature conditions and it is easy to turn the package. Compared with the use of paint, the tundish dry method overcomes the shortcomings of manual application. In particular, the substantial improvement in service life meets the requirements of continuous operation in the steel industry. It has been rapidly applied in recent years and has shown a trend of completely replacing tundish coatings.
Construction Method of Tundish Dry Ramming Material
-
Construction preparation
- ① First clean the tire mold and apply a layer of graphite powder mixed evenly with engine oil or water around it. Then let the tire mold air dry naturally, and place the vibration motor that can work normally on the tire membrane at the required position. After installation, carefully check whether it is firm to prevent the fasteners from loosening during use.
- ②Construction can be started after the tundish temperature drops below 50℃. The permanent layer must be clean, no residual paint or dust must adhere to it, and no water should be sprinkled into the tundish.
- ③ Prepare the paint to be used.
-
Construction method
- ①First install the tundish nozzle seat brick to ensure that its upper surface is on the same plane. Then pour the dry ingredients evenly into the bottom of the bag and pound tightly around the nozzle bricks. Tamper layer by layer or use plate vibration to tamp the bottom material of the bag. The material construction height requirement is slightly higher than the upper surface of the nozzle seat brick. This is conducive to full contact with the fetal membrane and bottom material.
- ②After the construction of the bottom bag is completed, place the tire mold into the middle bag. When setting the mold, make sure that the gap thickness between both sides of the tire mold and the permanent layer is the same.
- ③Pour dry materials into different positions along the side wall, and use vibration to drag them around the tire mold while pouring. Fully exhaust the dry material and reduce material segregation during the vibration of the fetal membrane.
- ④Construct layer by layer, until the dry material fills the entire gap and the height of the dry material, is higher than the height of the permanent layer.
- ⑤ Start the vibration motor in the tire mold, and the vibration time is 5-10 seconds. Then use an auxiliary manual vibration motor to vibrate along the tundish for a circle.
- ⑥Add dry materials to fill the gaps left by vibration, and fully compact or tamp the top dry materials.
- ⑦Ignite the burner in the tire mold for heating. The temperature of the tire mold is controlled between 200-300℃ and the heating time is 1-2 hours.
- ⑧Bake directly over high heat for about 1 hour before use. It can be used when the temperature reaches above 1000℃.

Application Advantages of Dry Ramming Materials for the Working Layer of the Tundish
- The service life is greatly improved.
The working layer of the tundish uses dry ramming mass materials. Due to the use of high-purity raw materials and the addition of special binders and additives, the service life of the dry materials is greatly increased, which can fully meet the requirements of high-efficiency and long-lasting continuous casting and pouring of steel.
- Heat insulation, heat preservation, and purification of molten steel.
Using dry tundish ramming material can reduce the temperature of the tundish steel shell by 30-40℃ compared with using magnesia coating material. This has a good effect on improving the operating environment, reducing heat loss of molten steel and preventing creep of the steel shell. At the same time, the tundish dry material is made of alkaline materials and added with special organic binders, which can reduce inclusions in molten steel and have a purifying effect on molten steel.
- Significantly reduce production costs and substantially improve subcontracting turnover efficiency.
The improvement of the service life of the dry ramming material in the tundish has significantly reduced the consumption of refractory materials per ton of steel. At the same time, the cutting of the billet is greatly reduced. In addition, the use efficiency of the subcontracting construction has been significantly improved. Compared with using magnesium coating, the number of tundishes is reduced by more than half, and the production efficiency is greatly improved.
- It’s easy to knock the bag off.
After the dry ramming material in the tundish is used, there will be a 20mm loose layer near the end of the permanent layer. The material shows its own properties, which is very beneficial for knocking bags. At the same time, it has a certain protective effect on the permanent layer of castables and steel shells.