Induction furnaces require refractory ramming materials. Furnace linings for different purposes have different requirements for refractory materials. Induction furnaces can only work effectively if ramming materials that meet smelting conditions are used. Rongsheng Unshaped Refractory Material Manufacturer can provide high-quality refractory ramming materials for induction furnace linings. Contact us for free quotes.
Requirements for the Performance of Ramming Material Refractory Materials in Induction Furnaces
Refractory materials for furnace linings should meet certain conditions to cope with the harsh working environment of the furnace lining. The refractoriness of steelmaking refractory materials should be ≥1700℃, and the refractoriness of smelting cast iron refractory materials should be ≥1500℃. The refractory materials used have good high-temperature stability, strong corrosion resistance, and small difference in basicity with slag. They have certain strengths at room temperature and high temperature. They have low resistance, good insulation, and low specific resistivity. The lining materials should avoid the introduction of ferromagnetic materials that can significantly reduce the specific resistivity and insulation of the materials. The lining materials have good thermal insulation properties, and the refractory materials used should be economical and environmentally friendly.
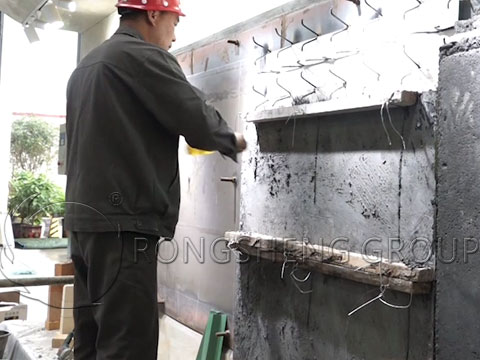
Functions of Each Component of Ramming Material
Ramming material is composed of refractory aggregate, refractory powder, additives, and other parts. Irregularly shaped aggregate particles are conducive to the interpenetration, bite and pinning between particles, which can improve the bonding strength. After sintering, refractory aggregate forms the skeleton of the material, which can improve the thermal stability and strength of the material. Refractory powder has a certain fluidity, which can fill the gaps in the material, increase the volume density of the material, and improve the construction performance. At the same time, the fine powder is more active than the aggregate particles, and can react with the additives in the material first, improve the strength of the material or improve other properties of the material. For amorphous refractory materials, the continuous particle gradation between refractory aggregate and powder has a great influence on the density of the material. It thus affects the volume density, porosity, strength and slag resistance of the material.
The function of the binder for ramming material is to bond the amorphous refractory material into a whole at room temperature or a certain temperature, with a certain shape and strength. The binder needs to have a large surface contact with the refractory aggregate and refractory powder, and at the same time, it is necessary to ensure the good volume stability of the material.
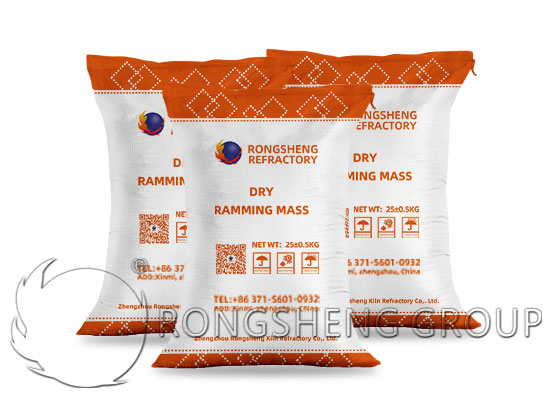
Classification of Ramming Materials for Induction Furnaces
According to different chemical properties, ramming materials can be divided into three categories: acidic ramming materials, alkaline ramming materials and neutral ramming materials. These three types of ramming materials have their own advantages and disadvantages.
- The main component of alkaline ramming materials is alkaline oxides. The widely used alkaline material is magnesium material, which has the advantages of corrosion resistance, high melting point, high load softening temperature, and no reaction with alkaline slag or alkaline melt. However, magnesium ramming materials have poor thermal shock stability and high sintering temperature. Thermal shock during work will cause cracking and peeling of furnace lining materials, which is only suitable for small-capacity induction furnaces.
- The main component of acid dry ramming materials is SiO2. In the case of other impurities, the crystal changes of SiO2 are relatively complicated, and the excessive heating rate of the furnace will greatly reduce the melting temperature of the material. Silicon dry ramming materials can be used for various induction furnace lining materials, and their use seems to be limited by refractoriness and purity.
- The main components of neutral dry ramming materials are neutral oxides or their complexes, such as Al2O3. Corundum dry ramming materials have the characteristics of high temperature resistance, good slag corrosion resistance, no effect on molten steel quality, short construction time, and no need for baking during construction. It can be widely used in various alloy steel smelting. At present, corundum dry ramming materials still have disadvantages such as low service life, difficult sintering, and difficult to control thermal expansion. Magnesium-aluminum spinel has good resistance to slag penetration. Adding fused magnesia sand to corundum materials to generate magnesium-aluminum spinel in situ can reduce the penetration of molten iron or slag into refractory materials and improve the slag resistance of materials. Aluminum-magnesium materials have secondary properties during use.
In addition, according to the type of material used, ramming materials can be divided into silicon ramming materials, corundum ramming materials, magnesium ramming materials, magnesium-calcium ramming materials, magnesium-aluminum ramming materials, aluminum-magnesium ramming materials, Al2O3-SiOC ramming materials, etc. According to different parts of use, ramming materials can be divided into tundish working lining, electric furnace bottom and power frequency melting groove dry ramming materials.
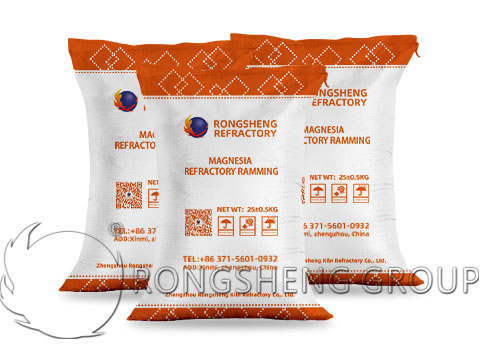
Reasons for Introducing MgAl2O4 into Refractory Ramming Materials for Induction Furnaces
- Advantages of acidic (siliceous) ramming materials: raw materials are cheap and easy to obtain. Disadvantages: During the heating process, SiO2 will undergo crystalline transformation, and its crystalline transformation is complex and usually accompanied by large volume changes. The furnace lining will be easily cracked, causing the furnace lining to be easily corroded by molten steel and slag, resulting in poor corrosion resistance. Acidic furnace lining materials are prone to slag-reducing reactions and have poor slag resistance.
- The advantages of neutral (corundum) ramming material: excellent high temperature resistance and slag corrosion resistance, no pollution to molten steel, short construction period, and the masonry lining does not need to be baked. Disadvantages: short service life, difficult to sinter, and difficult to control thermal expansion.
- The advantages of alkaline (magnesia) ramming materials: high softening temperature under load, high refractoriness, and excellent resistance to alkaline erosion. The SiO2 contained in the material will react with MgO during the heating process to form forsterite, which can block the pores and enhance the material’s slag resistance. Disadvantages: The material will crack and peel off the furnace lining due to thermal shock during service.
Many scholars have studied aluminum-magnesia ramming materials for induction furnaces. The MgAl2O4 generated by the reaction between Al2O3 and MgO during the heating process can block some pores. Moreover, MgAl2O4 will play a bridging role between Al2O3 and MgO, increasing the strength of the material, improving the material’s slag resistance and service life. Comparison of materials for neutral induction furnace linings and alkaline furnace linings.
Modern metal smelting is developing in the direction of large-scale containers. From the characteristics of the induction furnace lining, it can be seen that the use of corundum-spinel lining is conducive to the large-scale smelting container.
The service life of alkaline and neutral refractory linings is longer than that of linings of other materials. Most companies producing cast steel and special steel choose neutral or alkaline refractory materials to build induction furnace linings. Comparison of lining service life. The service life of linings built with materials containing magnesium-aluminum spinel is longer than that of linings of other materials.

Rongsheng Amorphous Refractory Manufacturer
Rongsheng Refractory Manufacturer is a powerful manufacturer and seller of refractory materials. Rongsheng manufacturer’s environmentally friendly and advanced fully automatic amorphous refractory production line has an annual output of 80,000 tons of amorphous refractory materials. It provides a reliable guarantee for the long life and integral lining of high-temperature industrial furnace linings. Rongsheng refractory manufacturer’s customers are spread over more than 120 countries and regions around the world, such as South Africa, Chile, Egypt, Colombia, Uzbekistan, Italy, Indonesia, Ukraine, Hungary, Spain, Kenya, Syria, Zambia, Oman, Venezuela, India, Peru, the United States, Ethiopia, etc. If you need to purchase refractory ramming materials and other refractory lining materials for high-temperature industrial induction furnace projects, please contact Rongsheng. Rongsheng manufacturer’s perfect customer service will not let you down.