Binder is a kind of amorphous refractory material, which is a material that binds refractory aggregates and powders and makes amorphous refractory materials strong. Aluminate cement is a kind of inorganic binder, which mainly makes amorphous refractory materials strong through the hydration of cement. Furnace Cement, aluminate cement is divided into calcium aluminate cement, barium chlorate cement and barium aluminate zirconium cement, among which calcium aluminate cement is the most widely used.
Chemical Composition and Refractoriness
Calcium aluminate is a hydraulically hardened cementing material made by finely grinding calcium aluminate clinker produced by sintering or melting. It has the characteristics of rapid hardening, high strength, fire resistance and resistance to sulfate erosion. According to the percentage of Al₂O₃ content, it can be divided into: CA-50 cement (50%≤Al₂O₃<60%), CA-60 cement (60%≤Al₂O₃<68%), CA-70 cement (68%≤Al₂O₃<77%) and CA-80 cement (77%≤Al₂O₃), etc.
The bonding properties of aluminate cement are mainly achieved by the hydration of calcium aluminate. The mineral composition of cement is different due to its different chemical composition. Furnace Cement Refractory Castables.
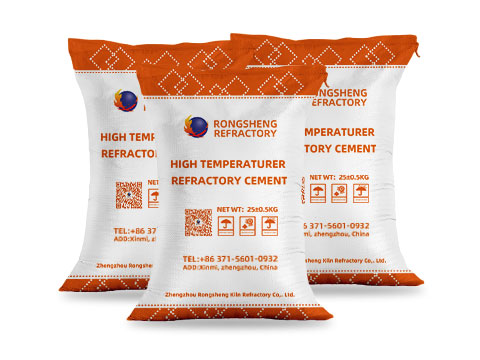
Advantages and Disadvantages of Aluminate Cement
Advantages
- Aluminate cement sets and hardens quickly. The 1d strength can reach more than 80% of the maximum strength, and is mainly used for projects with urgent construction periods, such as national defense, roads and special emergency repair projects.
- Aluminate cement has a large hydration heat and concentrated heat release. The hydration heat released within 1d is 70% to 80% of the total, which makes the internal temperature of the concrete rise higher. Even if it is constructed at -10℃, aluminate cement can set and harden quickly, and can be used for projects constructed in winter.
- Under ordinary hardening conditions, aluminate cement has a strong resistance to sulfate corrosion because the cement stone does not contain tricalcium aluminate and calcium hydroxide and has a large density.
- Aluminate cement has high heat resistance. If refractory coarse and fine aggregates (such as chromite, etc.) are used, heat-resistant concrete with a service temperature of 1300 to 1400℃ can be made.
Disadvantages
- However, the long-term strength and other properties of aluminate cement tend to decrease, and the long-term strength decreases by about 40% to 50%. Therefore, aluminate cement is not suitable for long-term load-bearing structures and projects in high temperature and high humidity environments. It is only suitable for emergency military projects (road and bridge construction), emergency repair projects (leakage plugging, etc.), temporary projects, and the preparation of heat-resistant concrete.
- In addition, aluminate cement mixed with silicate cement or lime not only produces flash setting, but also cracks and even destroys the concrete due to the formation of highly alkaline hydrated calcium aluminate. Therefore, during construction, in addition to not mixing with lime or silicate cement, it must not be used in contact with unhardened silicate cement.
Application of calcium aluminate refractory castables in aluminum melting furnaces
Refractory materials for aluminum melting furnace linings are usually kept at temperatures below 1000°C. Fluorspar or barite and other sintering aids and anti-wetting agents are added to these refractory materials to promote low-temperature sintering of the materials and improve resistance to aluminum liquid penetration. However, when the furnace is overheated for some reason, these additives can cause premature corrosion of the refractory materials.
In order to overcome the problem of premature corrosion of refractory materials for aluminum melting furnace linings, a calcium aluminate (CaO-Al2O3, abbreviated as CAA) refractory material with calcium aluminate as aggregate and calcium aluminate cement as binder was developed. Usually CAA is made by melting raw materials with a material ratio of Al2O3 and CaO CaO/Al2O3=1 or 0.7 (molar ratio), and crushed into different particle sizes. Since CAA is made by melting process, its apparent porosity is almost zero. In CAA materials, the mineral phase is mainly CaO-Al2O3, with a melting point of 1600℃.
Calcium aluminate cement (abbreviated as CAC) can be prepared by sintering and electric melting processes, and its chemical composition is about CaO 27%, Al2O3 71%.
The results of the comparative crucible self-etching test of CAA castables and ordinary castables at 800℃, 72h with AZ8GU aluminum alloy show that CAC-bonded castables have excellent anti-penetration ability. On the contrary, CAC-bonded plate-like alumina castables can be deeply penetrated into its structure by aluminum alloy melt, and there is obvious corundum (α-Al2O3) generation. The test results also show that the aluminum liquid penetrates deeply into the clay castable with anti-wetting agent, even the clay castable with CAA added.
It has been clarified that the interaction between the alloy melt and the refractory material in the aluminum smelting furnace is mainly the penetration of the melt into the pores in the structure of the furnace lining refractory material, resulting in the reduction of SiO2 and/or aluminum oxides to form corundum (α-Al2O3). In the case of sodium-rich alloys or treatment with sodium-rich alkali salts, β-Al2O3 is formed, causing the aluminum-rich refractory lining to peel off and prematurely damage. Since CAA materials are almost not penetrated by aluminum liquid, there is almost no problem of structural peeling and accelerated damage to the refractory lining.
The results of the comparative test also show that the permeability resistance of CAA low-cement castables without anti-wetting agents is the same as that of traditional alumina-based low-cement castables with BaSO4 (anti-wetting agent) added. Moreover, the former can be used at a temperature of up to 1350℃, which can ensure that even when the furnace is overheated, it will not cause premature corrosion of the refractory lining. This shows that CAA low-cement castables with CAA as aggregate and CAC as binder are fully compatible with the use conditions of aluminum smelting furnaces.
Another study, 500℃, 100h CO erosion test, the results show that the iron-free CAA has excellent CO erosion resistance after heating to 800℃. This shows that CAA castables with CAA as aggregate and CAC as binder can also be used in the petrochemical industry.