Refractory castables not only have high performance and good performance. Therefore, a large part of the boiler structure is made of refractory castables. In many cases, refractory castables can be modified to produce refractory materials with different properties. This is one of the reasons why refractory castables are so popular now.
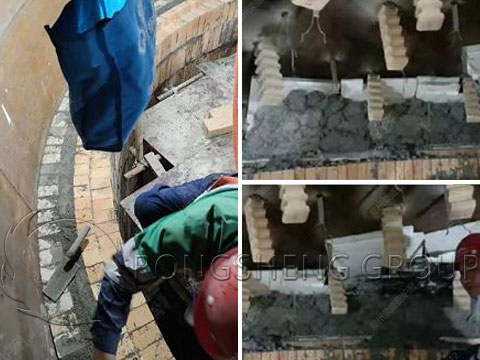
Causes of damage to refractory castables used in furnaces and castable repairs
The refractory castable for the furnace is in use. If used for a long time, it is easy to be damaged. There are also some products that are easily damaged during the curing process. When building boilers, the use of aluminate cement refractory castables is mainly caused by the combination of aluminate cement and castables.
1. Surface crushing caused by alkaline impurities.
The presence of soluble bases in materials increases solubility and accelerates reactions as important prerequisites. In cement refractory castables, increasing cement content and increasing system alkalinity will result in larger hydrated minerals, which favors reactions. Curing environment temperature and humidity are important factors in damage. Generally, the greater the humidity, the easier it is to wet the pores in the cast body. Under humid conditions, dissociation is easier and reactions are smoother. The density of the green body is also an important factor. When the porosity of the green body is high, water from the air is more likely to diffuse into the green body. The damage reaction continues into the depth of the green body, causing the surface and interior of the cast furnace lining to be crushed, thereby destroying the material. In addition, the shape and thickness of the blank also affect the reaction. Additionally, the quantity and quality of construction water can affect damage.
2. Surface powdering caused by carbonization reaction.
Surface chalking caused by carbonation reactions can be divided into two types. One is direct carbonation, where carbon dioxide reacts directly with the hydration products of cement to form a calcium carbonate-calcium aluminate complex. It closes surface pores and causes surface hardening, thereby inhibiting comminution. The other is catalyzed by sodium ions in the presence of soluble alkali metal oxides. This is similar to the mechanism of sodium ion damage, which can lead to failure of the castable.
The refractory casting damage repair method in the furnace is mainly used to solve surface damage:
- Clean high-purity raw materials and reduce the content of soluble alkali metals. When preparing refractory castables, choose high-quality refractory aggregates as much as possible, and choose washed and baked raw materials with low alkali content (such as bauxite and corundum). If the raw material is not calcined (such as andalusite), choose more carefully and try to use complex sodium and low-concentration mixtures. The dispersion effect and filling effect of micro powder are beneficial to increasing the density of castables. However, when selecting micro-powder, the impurity content of the micro-powder should be appropriately controlled to minimize the amount of cement containing high alkali metal impurities.
- Strengthen construction water quality control.
- Reduce the contact between the castable surface and air. Surface refractory coatings, coverings, etc. can be used to seal surface pores and minimize the diffusion of CO2 and water vapor into the castable to prevent damaging reactions.
- Accelerate hardening, dry the green body as quickly as possible, promote the development of green strength, and eliminate the conditions for damage reactions.
Time has shown that the furnace’s refractory pouring damage repair method effectively improves refractory damage. When using castables, we should take correct measures in time to carry out a good transformation of the boiler.