The purpose of ladle cover: Controlling the temperature drop of molten steel during transportation, refining and pouring has become a key factor in the innovation of the steelmaking industry in recent stages. The change of ladle thermal state is also one of the important factors for the converter to formulate the temperature compensation system of molten steel.
During the transportation, refining and pouring of the ladle, there are two main ways of heat loss. One is the heat conduction through the lining material of the ladle, and the other is the heat conduction and heat radiation of the upper molten steel in contact with the air. After the ladle is covered during the turnover of the ladle, it plays a good protective role in the heat dissipation of the ladle, and the thermal state of the ladle during the turnover process is more stable. It creates conditions for accurately controlling the temperature and temperature drop of the ladle, and also further reduces the heat loss of the ladle during the turnover process.
The ladle is covered throughout the process. The technology of covering the ladle throughout the process is adopted by some large steelmaking enterprises in China. Some steel mills have adopted technical measures such as covering the ladle throughout the process, improving the ladle turnover rate, and low-temperature high-speed casting. The temperature of the molten steel from tapping to the bottom of the ladle after ammonia blowing, the ladle hoisting process, and the casting process has been reduced by 20℃, 11.1℃, and 25.9℃ respectively. Some steel mills have also reduced the average tapping temperature of the converter by 10 to 30℃ through the process of covering the ladle throughout the process, which has increased the qualified rate of the middle ladle temperature of the continuous casting machine by 8%. Compared with the ladle baking for 8 hours, the temperature of the ladle lining increased by 8℃ when the ladle was left for 8 hours after the cover was added, creating conditions for converter production and energy saving and consumption reduction.
Application of Heavy-Duty Ladle Cover Castables on Ladles
Ladle cover manufacturers are accustomed to using heavy-duty castable structures, castable fiber blanket composite structures for insulation, and fiber blanket structures. These methods have solved the problem of molten steel temperature drop to a certain extent, but it is difficult to fundamentally solve the problem of light and long-life ladle covers. This has brought obstacles to the promotion and innovation of full-process ladle cover. The main reasons are as follows:
1) The density of heavy-duty ladle cover castables is heavy (2.8g/cm³). When hoisting and unloading at high temperatures, the metal frame that the working surface can withstand under the tensile force on the back has low mechanical properties under high temperature conditions, and the heavy-duty castable has low ability to withstand tensile force. When hoisting and unloading at high temperatures, the ladle cover convexly deforms, causing the upper cover plate of the ladle cover to bulge, thereby affecting the service life of the ladle cover. In addition, heavy-duty castables have poor thermal shock resistance and a large thermal conductivity, so the heat loss of molten steel radiation and conduction during use is large. The energy-saving effect of full-process ladle cover is not very ideal, which limits the development of ladle cover.
2) The energy-saving effect of using fiber folding blocks on the full-process ladle covering is manifested, and the density of fiber folding blocks is relatively low. However, under the high temperature state of molten steel radiation, the grain boundaries of refractory fibers are continuously filled with similar atoms (particles) and solid solution occurs during the growth of grains, so that the impurity enrichment at the sample boundaries is increasing. However, the impurities are irregularly arranged, have weak bonding force, and are highly sensitive to temperature changes. Therefore, the strength at the grain boundary is much weaker than the bonding between the lattices, causing stress to penetrate the grain boundary at the reduced diameter, causing the fiber rod to break (i.e., pulverization). Large chunks of fiber folding blocks fall off, and the high temperature of molten steel radiation burns the iron sheet of the ladle cover through the fallen fiber folding blocks, which also limits the development of full-process ladle covering.
In view of the above reality, combined with the development of the functionalization of lightweight high-strength castable products, the ladle cover lining was changed to a lightweight high-strength castable structure, and applied in a steel plant, achieving satisfactory results (more than 550 heats). Generally, the service life of ladle cover is 200-300 furnace times. Long life and energy saving are the requirements for the use of refractory materials. Lightweight and high-strength castables have brought the insulation work of ladle covering to a new level.
Physical and Chemical Properties of Lightweight High-Strength Castables
Early lightweight castables were mainly produced using fly ash, floating beads, ceramsite fiber, high-aluminum lightweight aggregate, etc. as aggregate powder. During use, its low operating temperature, poor thermal shock stability, and low strength restricted the development of lightweight castables. Lightweight high-strength castables use alumina-based corundum hollow balls as lightweight aggregates, calcium aluminate cement as a binder, homogenized alumina fine powder as a matrix, and introduce functional additives to enhance the thermal shock resistance and medium and high temperature flexural strength of the castable.
Take a steel plant using lightweight high-strength castable ladle capping as an example: the full-process ladle automatic capping system uses lightweight high-strength castables, and it has been determined that the tapping temperature can be reduced by 8℃ to 15℃. Take a 120-ton empty ladle of this steel as an example: the next batch of molten steel can be cooled by 17℃ to 19℃ within 20 minutes. Therefore, in order to keep the pouring temperature unchanged, the tapping temperature of the converter can only be increased, and this measure will bring great energy consumption and material loss.
From the above, it can be seen that the temperature drop of the molten steel from tapping to the end of refining is 90℃ when using lightweight high-strength castables and 99℃ when not covered. The temperature drop in this stage is 9℃.
The vacant time of the ladle covered with lightweight high-strength castables is within 4 hours, and no offline baking is required, and the ladle can be used in the converter. After using lightweight high-strength castables to cover, the temperature of the empty ladle drops by 300℃ after 9 hours of vacancy, and the ladle covering agent can be used after covering.
Results of Lightweight High-Strength Castable for the Entire Ladle
Structural characteristics of the ladle cover
After a detailed understanding of the use temperature and use environment of the steel plant ladle cover, combined with the characteristics and performance of lightweight high-strength castables, the ladle cover lining structure was identified as a vulnerable part. The center of the ladle cover, where the molten steel radiation is stronger, has a diameter of about 1.5 meters. 140mm lightweight high-strength castables are used, and the other parts use fiber blankets of 140mm. The anchors are mostly Y-shaped structures with a distribution spacing of 200mm and a total height of 70mm and 50mm.
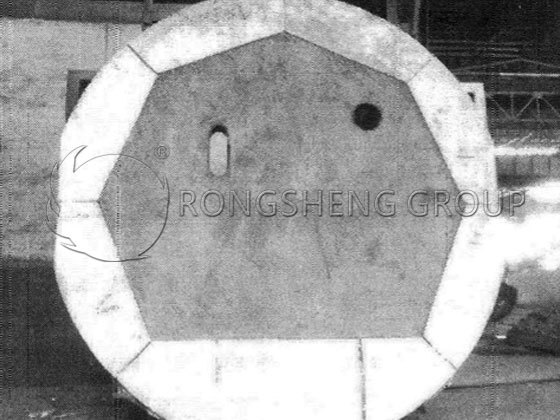
Advantages of using lightweight high-strength castables
- (1) It has excellent thermal insulation and insulation performance, no thermal expansion stress, and resistance to thermal shock and mechanical vibration.
- (2) It is light in weight, with an average volume density of only 1.7g/cm³. It can replace traditional heavy refractory materials, effectively strengthen the ladle cover insulation structure, and effectively reduce the load-bearing load of the ladle cover transmission structure.
- (3) The overall structure of the ladle cover lining is uniform; it is easy to construct and repair.
Scope of application
It can meet the needs of various industries, product forms and technical performance within the range of 300℃ to 1500℃.