Introduction: The Critical Role of Refractories in Industrial Boilers. Industrial boilers operate in extreme conditions, subjected to high temperatures and thermal cycling. To ensure efficiency and longevity, the right refractory materials must be selected to line these boilers. Refractories help contain and direct heat, improving energy efficiency and protecting the structural integrity of the boiler. Two of the most effective refractory materials for industrial boiler use are castable and plastic refractories. RS Monolithic Refractory Manufacturer will explore how castable and plastic refractories work, their unique properties, and why they are essential for industrial boilers.
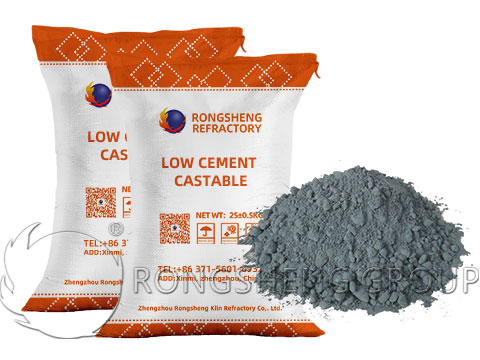

Castable Refractory for Industrial Boilers
What is Castable Refractory?
Castable refractory is a mixture of high-temperature aggregates, bonding agents, and additives that provide excellent resistance to thermal shock, erosion, and corrosion. These refractories are known for their high strength and the ability to form dense, durable linings that can withstand severe operational conditions inside boilers. The term “castable” comes from the fact that this material can be mixed with water and cast into specific shapes or applied directly to boiler surfaces.
Key Properties of Castable Refractory
- High-temperature resistance: Castable refractories are designed to withstand temperatures exceeding 1,800°C (3,272°F). This makes them ideal for the extreme heat generated in industrial boilers.
- Thermal shock resistance: Industrial boilers experience frequent temperature changes, which can cause refractory linings to crack and deteriorate. Castable refractories are engineered to resist these thermal cycles, maintaining their integrity over time.
- Durability and abrasion resistance: The abrasive nature of certain fuels and materials used in industrial processes can lead to rapid wear. Castable refractories offer excellent resistance to mechanical damage, prolonging the lifespan of the boiler lining.
- Ease of installation: One of the biggest advantages of castable refractories is their ability to be installed in place without requiring pre-formed bricks. This makes installation and maintenance more convenient, especially for complex or hard-to-reach boiler shapes.
Applications of Castable Refractory in Industrial Boilers
- Furnace linings: Castable refractory is commonly used to line the furnace chamber of boilers, where intense heat is generated.
- Burner blocks: Burner areas, subjected to direct flame impingement, benefit from the high-temperature resistance of castable refractories.
- Flue linings: Castable refractories are often applied to flue linings to protect against acidic gases and thermal wear.
- Boiler walls and arches: These areas require high thermal insulation and resistance to damage, making castable refractory the material of choice.
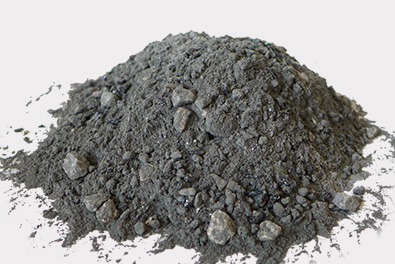
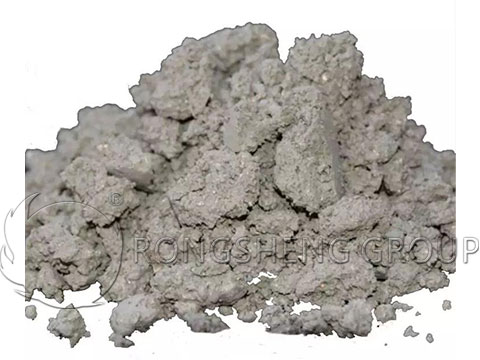
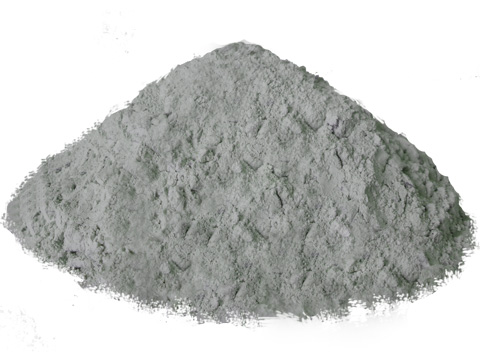
Plastic Refractory for Industrial Boilers
What is Plastic Refractory?
Plastic refractory consists of a mixture of high-quality refractory aggregates, bonding clays, and plasticizers, giving it a putty-like consistency. Unlike castable refractories, plastic refractories do not require water for installation. They are hand-packed into place and molded to fit irregular surfaces or tight areas, making them ideal for repairs or sections that are difficult to access.
Key Properties of Plastic Refractory
- Flexibility in installation: Plastic refractories are known for their versatility in installation. Because they can be manually shaped and packed into areas where rigid refractory shapes would not fit, they offer a solution for unique and complex boiler geometries.
- High-temperature capability: Like castable refractories, plastic refractories can withstand high temperatures, up to 1,700°C (3,092°F), making them suitable for most industrial boiler applications.
- Thermal expansion: Plastic refractories have a unique advantage in their ability to expand slightly when exposed to heat, creating a tight seal and reducing gaps or cracks in the boiler lining.
- Repair efficiency: Plastic refractories are often used for patching and repairing damaged refractory linings. They can be applied quickly without needing to dismantle entire sections of the boiler, saving time and minimizing downtime.
Applications of Plastic Refractory in Industrial Boilers
- Boiler tube protection: Boilers often have a network of tubes running through them to transport water or steam. These tubes are subjected to high heat and are prone to damage if not adequately protected. Plastic refractories can be packed around these tubes, creating a thermal barrier.
- Repairs and maintenance: When an industrial boiler’s lining experiences localized damage, plastic refractories are often used for on-the-spot repairs. Their moldability and ease of application make them a fast and efficient option.
- Sealing expansion joints: Boilers require expansion joints to allow for thermal movement. Plastic refractories can be used to seal these joints, ensuring they remain flexible while preventing heat escape.

Comparing Castable and Plastic Refractories
While both castable and plastic refractories are widely used in industrial boiler applications, each has distinct advantages based on specific operational needs.
- Installation: Castable refractories offer more flexibility for large surface areas or new construction projects due to their ability to be cast into shapes. Plastic refractories, on the other hand, are better suited for repairs or tight, irregular areas.
- Durability: Castable refractories tend to offer higher mechanical strength and durability, making them ideal for areas subject to high abrasion. Plastic refractories are less robust in abrasive environments but offer excellent sealing capabilities.
- Thermal properties: Both types offer excellent thermal resistance, though castable refractories often perform better in prolonged high-temperature settings, while plastic refractories excel in thermal expansion and sealing.
The Choice of Refractory Material for Industrial Boilers
Industrial boilers operate in extremely demanding environments, and the choice of refractory material can significantly impact their performance and longevity. Castable refractories provide robust, high-temperature-resistant linings that ensure durability and efficiency, while plastic refractories offer flexibility in installation and repair. Both materials play a critical role in enhancing the operational capabilities of industrial boilers, ultimately improving their energy efficiency and lifespan.
For any boiler application, choosing the right refractory solution—whether castable or plastic—can make all the difference in ensuring reliable, long-term performance.