Delivering High-Temperature Solutions to the World. With industrial operations becoming increasingly complex and demanding, RS Monolithic Refractory Manufacturer has risen to the challenge by supplying high-quality refractory materials to over 120 countries, including South Africa, Chile, Egypt, Colombia, Uzbekistan, Italy, Indonesia, Ukraine, Hungary, Spain, Kenya, Syria, Zambia, Oman, Venezuela, India, Peru, the United States, and Ethiopia. Our commitment to innovation and quality has made us a leader in providing cutting-edge refractory solutions, such as monolithic castables with high-temperature capacity for furnaces in foundry applications.
Foundries operate under some of the most challenging conditions, requiring materials that can withstand extreme temperatures, mechanical stress, and corrosive environments. At RS Monolithic Refractory, we understand these demands and deliver products that help industries maintain efficiency and safety in their operations. In this blog, we’ll explore the benefits and applications of our high-temperature monolithic castables for foundry furnaces and how our products have helped industries across the globe.
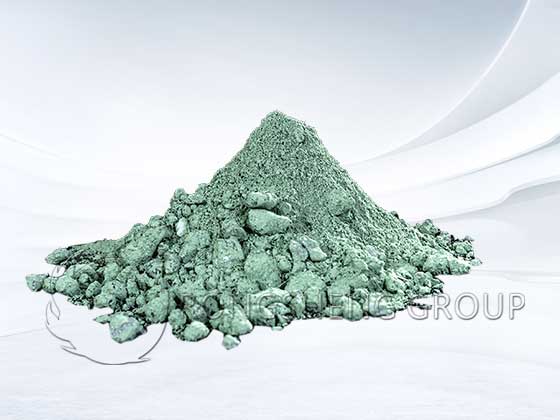
What Are Monolithic Castables and Why Are They Essential?
Monolithic Castables Explained
Monolithic castables are a type of unshaped refractory material that can be cast into place to form strong, durable, heat-resistant linings. Unlike traditional refractory bricks, monolithic castables are mixed and poured directly into the furnace or kiln, creating a seamless, highly durable lining that can withstand high temperatures, thermal shock, and chemical attacks.
At RS Monolithic Refractory, our castables are specially formulated to meet the extreme demands of foundry furnaces, where metals are melted and processed at high temperatures. The seamless lining created by monolithic castables offers several advantages, including greater flexibility in installation, excellent thermal insulation, and superior performance under the toughest conditions.
Why Foundries Rely on High-Temperature Castables
Foundry furnaces are subject to extreme thermal and mechanical stress due to the high temperatures required to melt metals like iron, steel, aluminum, and bronze. The monolithic castables provided by RS Monolithic Refractory are designed to withstand temperatures exceeding 1,600°C, making them ideal for foundry applications. These materials provide several key benefits, including:
- Thermal Stability: RS Monolithic’s high-temperature castables maintain structural integrity under continuous exposure to extreme heat, reducing the risk of cracks, spalling, or failure.
- Resistance to Abrasion and Wear: Foundries often face high levels of mechanical wear due to the movement of molten metals and mechanical equipment. Our castables are engineered for superior wear resistance, ensuring a longer service life for furnace linings.
- Chemical Resistance: Exposure to corrosive substances like slag, fluxes, and molten metal can degrade refractory materials over time. Monolithic castables from RS Monolithic offer excellent chemical resistance, protecting furnace linings from erosion and chemical attack.
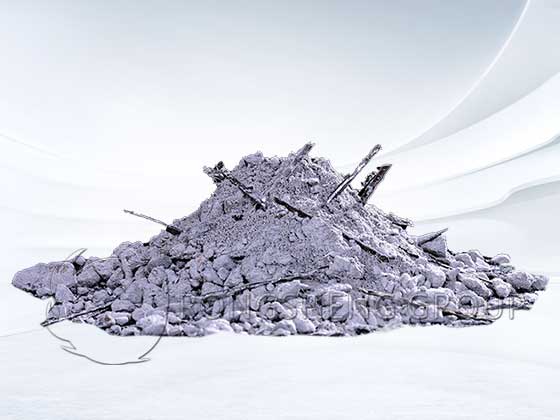
Applications of High-Temperature Monolithic Castables in Foundry Furnaces
Why Foundries Worldwide Choose Monolithic Castables
In foundries across the globe, monolithic castables with high-temperature capacity play a crucial role in ensuring safe and efficient operations. Foundry furnaces, including induction furnaces, cupola furnaces, and electric arc furnaces, require refractory materials that can withstand intense heat and mechanical stress without compromising performance.
RS Monolithic Refractory has supplied high-performance castables to foundries in countries like South Africa, Chile, Egypt, Indonesia, and Venezuela, where the demands on furnace linings are particularly stringent. Our monolithic castables are engineered for the following applications:
- Melting Furnaces
In foundries, melting furnaces are at the heart of the operation, reaching temperatures high enough to liquefy metals. Our high-temperature castables are used to line these furnaces, ensuring they can maintain operational efficiency while withstanding the stresses of continuous heating and cooling cycles.
- Holding Furnaces
After metal is melted, it is often transferred to holding furnaces, where it remains molten before casting. These furnaces require castables that can not only handle high temperatures but also maintain thermal stability over prolonged periods of operation. RS Monolithic’s castables ensure optimal energy efficiency by reducing heat loss and maintaining consistent temperatures.
- Ladles and Transfer Vessels
Molten metal is transported from one furnace to another using ladles or transfer vessels. These vessels must have linings capable of withstanding rapid temperature changes and the abrasive nature of molten metal. Our monolithic castables provide a seamless, durable lining that protects these vessels from thermal shock and wear.
- Furnace Repair and Maintenance
RS Monolithic’s castables are also essential for repairing and maintaining furnace linings. Their ability to be poured or troweled into place makes them a convenient and efficient solution for patching and repairing damaged areas of furnaces, minimizing downtime and reducing operational costs.
Global Expertise: Supplying Refractory Materials to Over 120 Countries
At RS Monolithic Refractory, our mission is to provide industries with high-performance refractory materials that stand up to the most demanding conditions. With more than 120 countries relying on our products, including Colombia, Hungary, India, the United States, and Ethiopia, our monolithic castables have become a trusted solution in foundries worldwide.
We pride ourselves on our global network of distributors and partners, ensuring that our customers receive the refractory materials they need, regardless of their location. Whether in a remote mining region in Africa or a major manufacturing hub in Asia, RS Monolithic’s products are delivered quickly and efficiently, allowing industries to maintain uninterrupted operations.

RS Monolithic’s Commitment to Quality and Innovation
Our success in over 120 countries is a testament to the quality and reliability of our products. Each batch of monolithic castables undergoes rigorous testing to ensure that it meets the highest standards for heat resistance, mechanical strength, and chemical durability. This commitment to excellence has made RS Monolithic a leader in the refractory industry, and our products are trusted by industries ranging from steel production to cement manufacturing.
Why Choose RS Monolithic Castables?
- Unmatched Performance: Our monolithic castables are designed for extreme durability, ensuring that furnace linings last longer and perform better under high temperatures and stress.
- Custom Solutions: We offer a wide range of castable formulations to meet the specific requirements of our customers’ foundry furnaces, from high-alumina castables to low-cement varieties.
- Global Reach: With a presence in over 120 countries, RS Monolithic Refractory has the infrastructure and expertise to deliver refractory solutions to any part of the world.
Conclusion: A Trusted Partner in High-Temperature Refractory Solutions
RS Monolithic Refractory Manufacturer is committed to providing industries worldwide with high-performance monolithic castables that ensure the efficient and reliable operation of foundry furnaces. Whether you are operating in South America, Europe, Africa, or Asia, our high-temperature castables deliver the performance, durability, and thermal stability you need for your foundry applications.
With more than 120 countries relying on our expertise, RS Monolithic is your trusted partner for refractory solutions. Contact us now to learn more about how our products can enhance the performance of your furnaces and help you achieve long-term success.