Dry ramming material refers to unshaped refractory materials that are constructed by ramming (manual or mechanical) and hardened under heating above normal temperature. It is made by mixing refractory aggregates, powders, binders, admixtures with a certain gradation and adding water or other liquids. According to the material classification, there are high alumina, clay, magnesia, dolomite, zirconium and silicon carbide-carbon refractory ramming materials. It is used to fill the gap between the furnace cooling equipment and the masonry or the filling material for the masonry leveling layer.
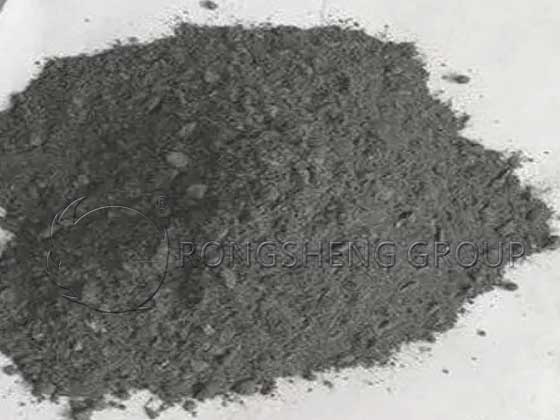
Magnesium Calcium Iron Dry Ramming Material
The mechanism of dry ramming of magnesium, calcium and iron. Magnesia electric furnace bottom dry ramming material has MgO as the main crystal phase and Fe2O3 as the sintering agent. At high temperatures, the main crystal phase and the binding phase diffuse through the grain boundaries and undergo solid solution reactions, forming some high melting point phases. This forms a hard shell – the sintered layer – on the bottom surface of the furnace. During the sintering process, Fe2O3 reacts with free CaO (f-CaO) to form 2CaO·Fe2O3 (melting point 1436°C), and the raw materials usually contain a small amount of impurities such as SiO2 and Al2O3. SiO2 reacts with f-CaO to generate C2S and C3S. Fe2O3 and Al2O3 react with f-CaO to generate C4AF (melting point 1415°C) and C2F. These two phases have low melting points and promote sintering of dry ramming materials. When the molten pool is sintered, the mixture containing C2F and C4AF can exert a sintering effect and form a ceramic bond as early as possible. As the power-on time is extended, the temperature becomes higher and higher, and the hard shell becomes thicker and thicker. When the sintered layer reaches a certain thickness, the furnace bottom slope will have high strength, good anti-penetration ability, anti-erosion and anti-scouring ability.
Characteristics of Magnesium Calcium Iron Dry Ramming Material
Because the main minerals of magnesia-calcium-iron dry ramming materials are high melting point phases such as magnesium oxide and calcium oxide. Therefore, the magnesia-calcium-iron dry ramming material has good resistance to high temperatures and slag corrosion, and can be quickly sintered and form a solid whole during use. Therefore, it has strong erosion resistance, good high temperature toughness, and is not easy to float during use.
The effect of using magnesium calcium iron dry ramming material. From the on-site use results, it was found that the magnesia-calcium-iron dry ramming furnace lining has a slow erosion rate and strong replenishability. It can significantly reduce the labor intensity of repairing and dismantling the furnace lining, directly improves the economic benefits of the steel plant and reduces the cost. At the same time, the time for changing the furnace shell is reduced, the production rhythm is accelerated, and the efficiency of the electric furnace is improved.
Production Technology of Magnesium Calcium Iron Dry Ramming Material
Production process: The production process of high-ferromagnesia-calcium sand is very simple. As long as natural magnesite, dolomite, light burned magnesium or other CaO-containing raw materials and Fe2O3-containing raw materials are mixed in a certain proportion (to meet the chemical mineral composition requirements after burning). After fine grinding, pressing into balls (blanks), and high-temperature calcining in a vertical kiln, rotary kiln or tunnel kiln, high-ferromagnesia-calcium sand can be produced.
Application of Magnesium Calcium Iron Dry Material in Tundish
Medium package coating and dry ramming materials. Medium-sized dry materials are made of high-quality magnesia (or magnesia-calcium sand) as the main raw material, and are processed by adding binding agents, sintering agents, and modifiers. Has good adhesion with permanent lining. It will not burst or peel during the baking process, and has good corrosion resistance. Features include easy removal of the bag after use. The dry material is mainly a dry ramming vibrating material in the middle. This dry material is actually added with solid resin or some inorganic solid binders.
After the installation of grinding tools and vibration ramming, the bonding agent in the dry material is liquefied or solidified through the hot internal mold to increase the strength. Then unmold and bake over high heat for use. Now the results of 77.5h and 147 heats have been obtained. Its density and other properties are higher than those of current general coatings, but there is still a certain gap between cast plates and high-density coatings.
However, dry tundish ramming materials can easily be made into magnesium-calcium tundish linings with very good results. In general, the CaO in wet magnesia-calcium coatings is mostly added in the form of CaCO3 and slaked lime. CaCO3 can only be decomposed when the temperature is above 1000°C, which is detrimental to the baking and service life of the tundish.
Types of Dry Ramming Materials
Types of dry ramming materials are. Acidic ramming materials (silica sand, silica and zircon). Neutral ramming material (corundum, mullite). Alkaline ramming materials, (magnesia, magnesium aluminum) and carbon and silicon carbide ramming materials (corundum-silicon carbide-carbonaceous, alumina-carbonaceous, magnesium oxide-carbonaceous, magnesium oxide-calcium oxide- Carbonaceous, etc.)
On cored induction furnaces, neutral dry ramming materials are generally used for the furnace body. The material of the dry ramming material used by the sensor changes with the conditions of use. In non-ferrous metal smelting furnaces, neutral dry ramming materials are often used. In ferrous metal smelting furnaces, alkaline or neutral dry ramming materials are often used. Dry ramming materials can be constructed using direct vibration or indirect vibration. The direct ramming method uses a vibrator to directly ram the refractory material. After fully vibrating a layer of refractory material with a tamper, rake its surface, then fill it with a new layer of material, and then fully vibrate it with a tamper. This is done layer by layer until the construction is completed. Although this method is time-consuming, it can avoid delamination between layers. Indirect vibration is the vibration force generated by the ramming device fixed on the inner or outer mold, and then transmitted to the refractory material through the template, thereby densifying the ramming material.