Low-cement castables are prepared from refractory aggregates, high-aluminum fine powders, and binders in a certain proportion, prefabricated, and baked into refractory materials with good performance. It is very suitable for the operating conditions of the heating furnace. Next, Rongsheng refractory manufacturers will introduce the application and use the effect of low-cement castables in the heating furnace according to the specific working conditions of the heating furnace.
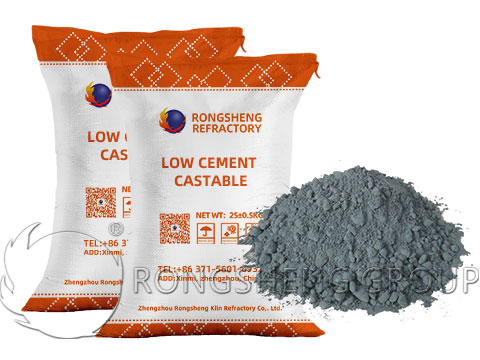
Working conditions of heating furnace
The original heating furnace was built with a large number of ordinary clay bricks, and some parts also needed to be processed, resulting in poor integrity of the masonry and reduced strength of the masonry. In particular, debris such as broken bricks falls into the gap between the trolley and the side wall. When the trolley enters and exits, the side wall is scraped and damaged. The damage to the furnace wall is very serious. In addition, when the masonry at the lower part of the arch foot of the furnace top is used for a long time, it will incline inward to create a gap, and the flame will directly burn the arch foot beam, which will cause great damage to the furnace body and needs to be repaired frequently. The service life of the kiln is about one year, which increases the maintenance cost and also affects the normal production of the hydraulic press.
A company built seven new forging furnaces, and the long-term use temperature is 1250 ℃. Among them, 4 are trolley furnaces, and 3 are double-chamber heating furnaces. The lining refractory materials are all low-cement castables. The inner lining of the trolley-type heating furnace adopts the anchor brick structure, and the top of the furnace is in the form of a flat roof hanging. According to the size of the furnace, the tire membrane is rammed and formed on-site, and the refractory materials of the furnace body are baked and put into use. The low-cement castable not only overcomes the low high-temperature strength of ordinary castables but also makes up for the defect of poor medium-temperature strength of ordinary castables. It uses superfine powder and high-efficiency admixtures, reduces the amount of cement and water, improves the pore structure to make it homogeneous, and increases the strength. The material has the characteristics of anti-penetration, corrosion resistance, impact resistance and wear resistance, good mechanical properties, and has a wide range of applications.

Material configuration and construction method of low cement castable
- (1) Material requirements. Using high-aluminum materials, the Al2O3 content is above 70%, and the refractoriness is 1770 °C. Coarse aggregate size requires 5~10mm, fine aggregate size requires 0.15~5mm, and the particle gradation ratio is uniform and good. In this way, the castable can have better compactness and high-temperature performance.
- (2) High aluminum fine powder. It is made of high-aluminum clinker, and the particle size requirement is less than 0.088mm and should not be less than 85%. The particle size of the fine powder has a direct impact on the properties of the castable, and the compressive strength increases with the increase of the specific area of the powder. However, it has an adverse effect on the thermal stability of the castable, and the dosage should not be too much.
- (3) coagulant. Using high alumina cement, the grade is not less than 625#, and the refractoriness is not less than 1400℃.
- (4) Water. Use clean tap water. The water content of low-cement castables is reduced from 10%~15% of ordinary castables to 5%~8%, and the amount of cement is also reduced from 15%~20% to 5%~8%.
The construction method of low cement castable
Mix the 50kg bagged low-cement castable mechanically, add an appropriate amount of clean tap water, and hold the mixed material tightly by hand to form a ball. The inner side of the furnace shell steel plate shall be built with fiberboard, lightweight refractory bricks, and anchor bricks as required, and then the formwork shall be supported for construction. The castable should be constructed continuously, and each layer of paving should not exceed 300mm. When vibrating, the vibrating rod kiln is fast inserted, gently dialed, and moved slowly. Pay attention to prevent the vibrating rod from causing voids and affecting the pouring quality. Expansion joints shall be reserved for the castable according to the design and specification, and one expansion joint shall be reserved every 2000mm. During construction, the expansion joints are filled with expansion tiles of the same width as the furnace wall. Because the expansion tile is in the shape of breaking waves, it can prevent the flame from entering and damaging the furnace shell. After 48 hours of natural curing, remove the template, and carry out a strict oven according to the oven curve.
Since the low cement castable has very good compactness, the oven is an important link before the castable is used, which is related to the service life of the furnace. The oven curve and method must be carefully formulated according to the thickness of the castable used, the molding method, the construction season, and the exhaust conditions. Especially in the low temperature holding time of 150 ° C and 350 ° C, the free water and crystal water in the castable should be completely discharged.
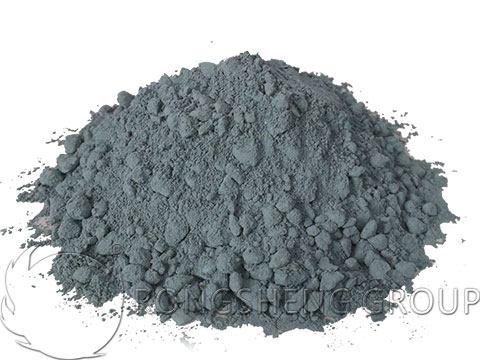
The use effect of low cement castables
Through the observation of the use of low cement castables in the heating furnace for many years, the overall performance of the furnace body is very good. The surface does not fall off, the refractory material of the furnace body is basically not damaged, and the surface temperature of the furnace shell is about 70 °C. The unit gas consumption of forgings is also reduced from 5300m3/t to 3500m3/t, which has achieved good economic results. The use of low-cement castables in kiln projects not only reduces the number of bricks used but also improves the labor intensity of construction and shortens the construction period. In addition, the castable lining has good integrity and excellent thermal insulation performance, which greatly reduces energy consumption, thereby achieving the effect of energy saving and emission reduction. Compared with clay bricks, the price of castables is 3 times that of ordinary furnace linings, but the service life of the kiln is increased by 5 times, and the economic benefits are obvious. In addition, the castable only needs a small number of furnace builders in the construction, which can save a lot of labor costs.
Advantages of using low cement castables
With the continuous development of refractory technology, the kiln is built by the way of prefabricated building blocks. The advantage is that the refractory castable prefabricated parts are produced and baked in the refractory material factory, and are directly installed at the use site, which greatly shortens the construction period and eliminates the need for ovens. In particular, for the use of hanging furnace beams, all the hanging parts on the top of the furnace are canceled, which saves 1/5 of the cost of building the furnace. The efficiency and economic benefits of the furnace are very obvious.