As the name suggests, low-cement castables are castables with low cement content, low cement dosage, and small calcium content. The lower the calcium content, the lower the pores and the stronger the erosion resistance. Low-cement castables are divided into low-cement castables such as aluminum silicate, mullite, corundum, magnesia-aluminum, fine stone, carbon, and silicon carbide. Low cement castables of different materials have different uses. Silicon carbide low cement castables are divided into blast furnace tap trough castables and steelmaking ladle castables.
Common Low Cement Castables
The most common low-cement castable is aluminum silicate, which is high-aluminum and low-cement castable. The cement content of high-aluminum low-cement castables is between 3% and 6%. If the cement content is 1%, it is ultra-low cement castables, and there are also cement-free castables.
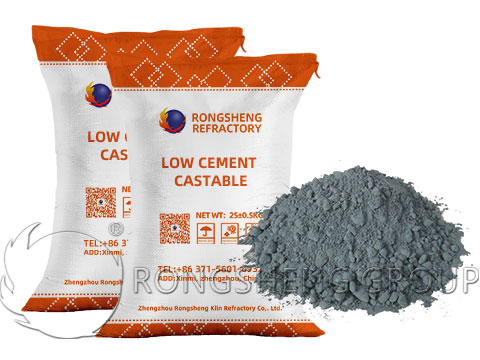
Clay and high-aluminum low-cement castables are most commonly used in heating furnaces and soaking furnaces. They are also used in heat treatment furnaces for building materials and some parts of the lining of rotary kilns. Low cement castables can also be used as high-temperature burner linings and heating furnace water cooling pipe wrapping linings. Lining bodies such as blast furnace tap trough, iron furnace tap trough, integral powder spray gun for molten iron pretreatment, etc. Corundum and chromium-containing corundum low-cement castables are used as linings in certain parts of refining equipment outside molten steel furnaces. It is also used in the lining of power frequency induction furnaces, the high-temperature wear-resistant lining of petrochemical catalytic cracking reactors, etc.
Low-cement castables are also continuously updated by manufacturers, further upgraded, and the formulas and gradations are adjusted. At present, many manufacturers use micron powder and ultrafine powder technology. The biggest feature of the result of cement bonding and micro-powder technology is high strength. As the heating temperature increases during use, the strength gradually increases.
It should be noted that low-cement castables have poor air permeability and may easily cause peeling or cracking during the baking process. The baking system should be reasonably formulated according to its material, construction thickness, and construction location. At the same time, metal aluminum powder, organic fibers, etc. can also be added to the castable. Making it easier to expel moisture to extend the service life of the low cement refractory castable lining.
Low Cement Castables Have a Wide Range of Uses
Low cement castables are suitable for linings of heating furnaces, various heat treatment furnaces, electric furnace covers, shaft kilns, rotary kilns, blast furnace tapholes, ladles, ladles, etc. Self-flowing low-cement castable is suitable for lining high-temperature refractory components with metal anchors. Such as the water-cooled tube lining of the heating furnace, the integral spray gun lining for spray metallurgy, and the impregnated tube lining of the RH and DH vacuum degassing devices. Ladle gas supply components and high-temperature wear-resistant linings for petrochemical catalytic cracking reactors, etc. Used in the construction of complex structural parts, which can greatly improve the overall use effect.

Low-cement castables are produced by adjusting the formula during the production process to reduce the CaO content, improve the overall performance of the castables, and increase the service life of the lining. Rongsheng monolithic refractory material manufacturer specializes in the production of monomorphic refractory materials for high-temperature industrial furnaces. Not only can we provide low-cement castables of various materials, but we can also provide designs of refractory lining materials. If you want to know more about low cement castables, you can contact us by email, or leave a message in the message box at the bottom of this article. We will contact you shortly. And will provide you with detailed information about low-cement castables for kilns.
What are the Differences between Low-Cement Castables and Traditional Castables?
Low cement castables are very different from traditional castables, mainly in the difference between mid-term strength and late-stage strength. Traditional castables have poor medium-term strength, while low-cement castables are far superior to traditional refractory castables. Not only is the cement dosage low and the calcium content low, but it also uses ultrafine powder technology to distribute the castable particles in a reasonable proportion. Moreover, the late-stage strength and mid-term strength of the castable are further improved.
Compared with traditional refractory castables, low-cement castables have higher density, lower porosity, and higher room-temperature curing strength. It also has good volume stability. Moreover, after drying and calcining, the volume shrinks slightly. The high-strength low-cement material in low-cement castables is formulated with pure calcium aluminate cement as the binding agent. The maximum service temperature of high-strength castables reaches 1600°C, and it has good wear resistance at high temperatures. High-strength, low-cement castables are suitable for use in various kiln linings with high temperatures and strong corrosiveness.
The low-cement material using fused white corundum as aggregate is called low-cement corundum castable. Corundum low-cement material has high mechanical strength, erosion resistance, and abrasion resistance, and the maximum operating temperature reaches 1700°C. Low cement corundum castable is suitable for use in large cement kiln mouths, multi-cylinder cooler elbows, and other lining parts where the temperature is above 1400°C and where impact erosion is severe. It is suitable for use in all parts of the kiln lining exceeding 1400°C.
Traditional refractory castables are made of refractory particles and powders, as well as high alumina cement. The particle gradation of the aggregate part is not as fine as that of low cement materials. The cement particles are also coarser, and the proportion of cement added is large, and the amount of water added during construction is also large. In addition, the cement dosage is large and the particles are not classified, so the cement material cannot be fully hydrated. Especially at a temperature of 800°C, there is no strength, so the performance of traditional castables is not as good as low-cement castables.