The intermediate frequency furnace ramming refractory material uses high-quality corundum as the main raw material. Composite materials such as various binders and special performance micro powder materials, high-temperature resistant binders, anti-cracking agents, anti-seepage agents, etc. are finely proportioned and mixed. The intermediate frequency furnace ramming mixes materials are all made of special high-grade materials, which have better performance in many aspects such as softness, refractoriness, slag resistance, erosion resistance, and thermal shock performance. Therefore, it is determined and ensured that this material can be used as a high-quality furnace lining material with stable and excellent performance under harsh or even harsh smelting conditions.
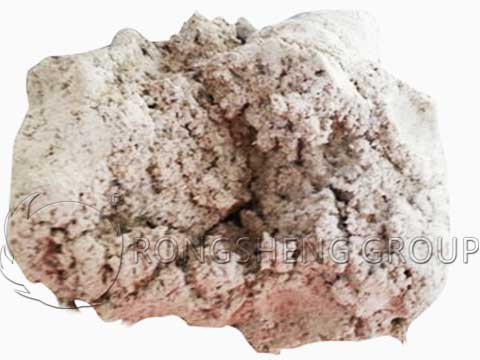
Intermediate Frequency Furnace Ramming Material
The intermediate frequency furnace ramming material has a series of advantages such as erosion resistance, strong stability, no cracking, strong operability, and high refractoriness. The intermediate frequency furnace ramming mixes material is a high-grade aluminum-magnesium refractory material, and the material is neutral and weakly alkaline. Intermediate frequency furnace ramming refractory material is suitable for smelting nickel-iron alloy, molybdenum-iron alloy, chromium-iron alloy, vanadium-titanium alloy, and titanium-tungsten alloy. Copper, aluminum, zinc alloy, plain carbon steel, high manganese steel, alloy steel, alloy cast iron, high-speed tool steel, and stainless steel, etc.
Precautions for the use of silicon carbide anti-corrosion ramming materials. The site or mixing equipment must be cleaned up before mixing. It is strictly forbidden to mix other impurities, especially steel shavings, and iron. It is strictly forbidden to mix into the material. After stopping the furnace, add a furnace cover and slowly cool down. The intermediate frequency furnace corundum ramming material is used continuously under normal construction, normal furnaces, and normal operating conditions, and more than 150 furnaces can be used for normal furnaces. Construction method, dry vibration, or dry pounding.
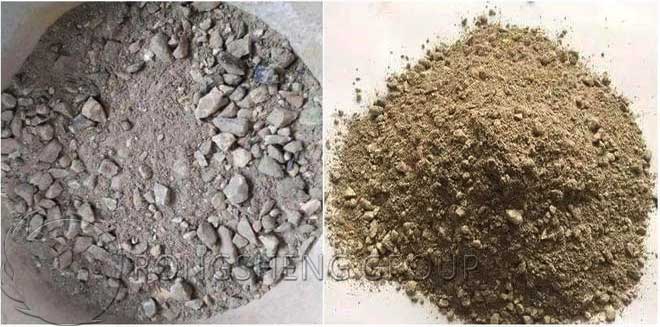
Silicon Carbide Ramming Mass
Silicon carbide ramming material is mainly used as the lining of coreless induction furnaces for melting and heat preservation of iron, steel, and non-ferrous metals. It is a mixture made of quartz as the main raw material and a small amount of sintering agent. Sintering agent compounds include boric acid, alkali metal borates, alkali metal phosphates, alkali metal silicates, and the like. These compounds have the effect of promoting sintering at medium and low temperatures.
Silicon carbide ramming refractory material has the characteristics of stable chemical properties, high-temperature resistance, wear resistance, erosion resistance, and corrosion resistance. Silicon carbide has high thermal conductivity, 64.4W/(m·K) at 500°C, and can transfer heat quickly.
Silicon carbide ramming material is made of high-purity, large-grain silicon carbide, corundum, chrome corundum superfine powder, aluminum chromium phosphate binder, and admixtures under specific conditions. It is an air-hardening ramming refractory material, which can be solidified in the air. The formation of its strength is due to the dehydration and concentration of the colloidal binder at a temperature of 35 ° C to 240 ° C, and the polymerization reaction. And produce a chemical combination of silicon carbide, corundum, and micro powder.
The silicon carbide ramming material can weaken the erosion of the furnace lining by alkaline substances due to the addition of a resist with high hardness and good corrosion resistance in the ramming mixes material. The slag resistance is good, which can make the thinner liquid slag hang a layer of slag on the furnace lining to form a slag film to protect the furnace lining. The product has high strength and good corrosion resistance to solid particles and liquid slag.
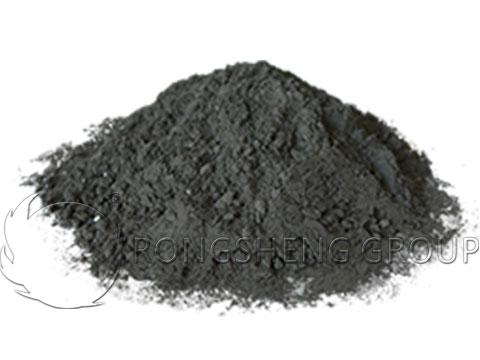
Silicon Carbide Ramming Material Product Performance
Silicon carbide ramming material is mainly made of silicon carbide, graphite, and anthracite. It is an amorphous refractory material made by adding additives such as superfine powder, and fused cement or resin as a binder.
Silicon carbide ramming material characteristic
- Good chemical stability.
- High-temperature resistance and good wear resistance.
- Good erosion resistance and corrosion resistance.
- High thermal conductivity.
The use of silicon carbide ramming material. It can be used to fill the gap between the blast furnace shaft cooling equipment and the masonry or the masonry leveling layer as a filling material or a caulking material. It can also be used as kilns for steelmaking, ironmaking, electric power, and non-ferrous metal melting furnaces.
Properties of silicon carbide ramming refractory mass. The silicon carbide ramming material has a density of 2.6g/cm3 and a compressive strength of 35MPa at 200°C. 60MPa at 800°C, maximum working temperature 1750°C, chemical composition: Si°C 89%, maximum particle size 3.0mm.
Construction method, the product is constructed in the form of pounding. Manual or mechanical ramming can be used according to the construction environment, and the hardening characteristics of the mixture after ramming are formed. Hardening and sintering are promoted in different ways. The performance of the ramming refractory material is not much different from that of refractory bricks and castables. It is convenient for construction and can resist the erosion of slag and gas.
1. Preparation of raw materials
Mix and prepare according to the ratio of 5.5kg of aluminum phosphate solution and 94.5kg of silicon carbide grade ingredients. The mixing preparation work needs to be carried out in a forced mixer. In order to make the consistency of the silicon carbide material easy to spread, 0.3L of water can be added per 100kg of material.
2. Ramping construction
Silicon carbide ramming mass is a smearing ramming mixes material. The design of the boiler requires a thickness of only about 12mm, and the process of one-time laying and one-time ramming should be adopted during construction. If due to the influence of climatic conditions, there are fine cracks on the surface of silicon carbide, as long as the cracks are not larger than 3mm, it is not necessary to take measures.
3. Maintenance of furnace lining
(1) Air drying (natural conservation). After the silicon carbide refractory lining is laid, it needs to be naturally cured first. Under the condition that the ambient temperature is about 20°C and the relative humidity is less than 75%, the silicon carbide furnace lining is air-dried by using chimney wind and natural ventilation.
(2) Heating and drying (hot water drying). Increase the temperature to 80~120°C with warm water through the piping system for not less than 12 hours.
(3) Heat treatment stage. The solidification of the aluminum phosphate chemical binder in the silicon carbide mixture and the high-temperature physical and chemical changes (cementation and adhesion, inorganic polymerization, and sintering) is mainly completed in the heat treatment stage of the furnace lining. The low-temperature heat treatment of the furnace lining can be completed at the initial stage of the boiler ignition blowpipe, and the temperature is increased to 300 °C for more than 24 hours. Further high-temperature heat treatment needs to be completed in the high-load stage of the whole set of unit startup. When the temperature increases to above 600°C, it should be controlled between 650~1000°C and the temperature rise rate should be controlled below 50°C/h.
The silicon carbide ramming refractory material is in good condition after more than 2 years of actual use. The combustion chamber and the secondary combustion zone have strong integrity. There are many refractory material factories in China that can supply silicon carbide and its products. Some construction units have self-assembled construction according to the requirements of the regulations, and the results are very good.
Rongsheng Monolithic Refractory Manufacturer
With intermediate frequency furnace ramming refractory material, silicon carbide ramming mixes material, and silicon ramming material, Rongsheng monolithic refractory manufacturers can provide high-quality monolithic refractory products. What should I do if the refractory material cracks, falls off, and is easy to wear? To completely solve the problem, we need to dig out from the root and analyze the real reason. Rongsheng manufacturers specialize in refractory production, research, and development services. Years of experience in production and sales can solve various difficult problems in the lining of high-temperature kilns. Contact us for a free refractory lining solution.