The application of heating furnaces is very wide, such as steel smelting, petroleum, chemical industry, and so on. No matter what industry it is used in, refractory materials are an indispensable and important component of heating furnaces. The traditional heating furnace lining uses low-cement castables, but the loss of low-cement castables is faster. At present, the application of high-alumina refractory plastics in heating furnaces has almost replaced low-cement castables.
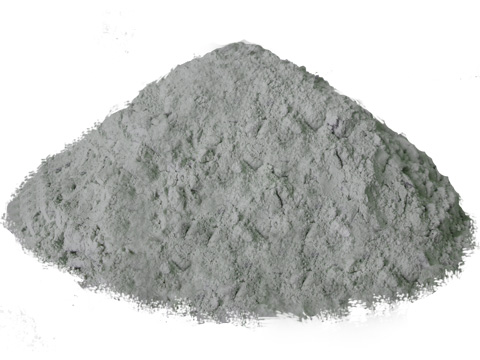
Damage Mechanism of Heating Furnace Lining
There are many types of heating furnaces, and the most used is the continuous heating furnace. The heating furnace has a complex structure and is continuously produced. The furnace is mainly divided into preheating zone, heating zone, and soaking zone. The damage to the furnace lining mainly comes from the erosion of the furnace atmosphere on the furnace lining and the impact caused by temperature changes and airflow. Using traditional low-cement castables, the aggregate expands greatly after high temperature, which is easy to cause cracks and peeling of the furnace lining. Moreover, the low-cement castable has poor corrosion resistance to acid gas.
Application of High Alumina Refractory Plastic in Heating Furnaces
In the selection of refractory plastics for heating furnaces, high-aluminum refractory plastics are mainly selected. High-alumina refractory plastics are mainly made of high-quality high-alumina aggregates, alumina powder, chemical binders, etc. in a certain proportion. High-aluminum refractory plastics have high plasticity. The application of high-aluminum refractory plastics in the heating furnace can make up for the lack of performance of refractory castables and improve the service life of the furnace lining.
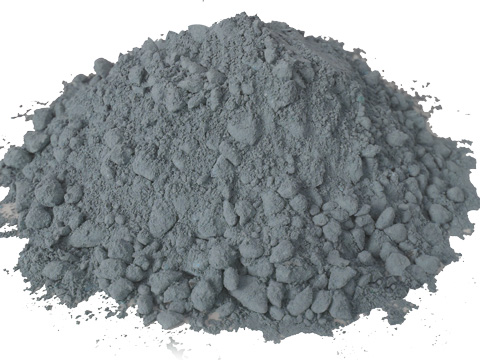
Construction and Oven of High Alumina Refractory Plastics
1) Construction
- ① Preparation before construction. Before construction, the quality of refractory plastics and anchoring bricks should be sampled to ensure that the performance indicators of the materials meet the standards. The tools used for construction and the surface of the construction body should be kept clean.
- ② mold support. The bottom formwork should be kept 5-10mm apart from the anchor bricks.
- ③ pounding. The ramming is carried out with a ramming hammer, and the direction must be perpendicular to the template to ensure at least one round-trip ramming. Use a wooden hammer or an air hammer (50mm to 70mm thick for each layer) to tamp it. Hair must be shaved between layers. If the construction is stopped in the middle, the ramming layer that has been constructed must be shaved.
- ④When the anchoring brick is installed, it must be ensured that it is tightly combined with the plastic.
- ⑤ Demoulding. Generally, the demoulding time is carried out within 4h after the construction is completed. At the same time, the kiln is done with surface shaving, expansion joints, and pores.
2) Oven-Drying
In order to obtain a furnace lining with long service life, in addition to the above-mentioned material selection and construction, the oven is also a key part. The main purpose of the oven is to discharge the free water of crystal hydration in the refractory plastic. Don’t be in a hurry during the oven process. If the oven is too fast, the water vapor in the masonry will be blocked, which will easily cause cracks or peeling, which will affect the use of the later heating furnace. Therefore, the oven process must strictly follow the oven curve of the refractory plastic.
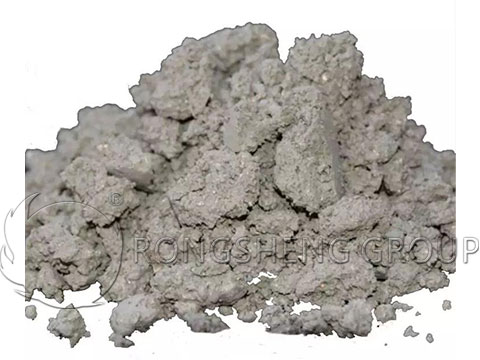
Applications of High Aluminum Refractory Plastics
The service temperature of refractory plastics varies mainly according to the quality of the granular and powdery raw materials used. For example, ordinary refractory plastics can be used below 1300℃~1400℃, high-quality refractory plastics can reach 1400℃~1500℃, chrome plastics can reach 1500℃~1600℃, high alumina corundum plastics can reach 1600℃~1700℃, or even higher. The furnace lining of the boiler needs to be made of high wear-resistant plastic.
It is very convenient to use refractory plastics for the repair of defective parts in the lining of circulating fluidized bed boilers. In addition, it is mainly used in various heating furnaces, soaking furnaces, annealing furnaces, sintering furnaces, and electric furnace tops in the iron and steel industry as linings.
When used in industrial furnaces, it must be used in conjunction with non-metallic or metal anchors. That is to say, anchors and supports must be added to the tamped refractory plastic lining so that the advantages of refractory plastic performance can be exerted and its service life can be improved.

The Service Life of High Aluminum Refractory Plastics
There have been many cases of using high-alumina refractory plastics to construct heating furnaces, and their service life is more than twice as long as that of cement castables. The general life of castable furnace lining is 2 to 3 years, while the use of high-aluminum refractory plastics can be used for more than 7 years. The surface of the furnace lining has been kept flat, and there is no obvious damage.
The price of refractory plastics is much higher than that of refractory castables. However, from the perspective of the service cycle, its cost performance is also much higher than that of the refractory castable lining. Therefore, refractory plastics have replaced refractory castables as the lining of heating furnaces, which has become an ideal choice for many iron and steel smelting and petrochemical enterprises. Contact us for free samples and quotes.