Refractory mortar is referred to as refractory clay or fire mortar, which is composed of refractory powder, binder, and admixture. Almost all refractory raw materials can be made into powder used to prepare refractory mortar. The ordinary refractory clay made of refractory clinker powder and an appropriate amount of plastic clay as a binder and plasticizer is called ordinary refractory clay, which has lower strength at room temperature, and higher strength is formed by ceramic bonding at high temperatures. The chemically bonded refractory clay, which uses hydraulic, air-hardened, or thermosetting bonding materials as the bonding agent, undergoes a certain chemical reaction and hardens before it is lower than the ceramic bonding temperature.
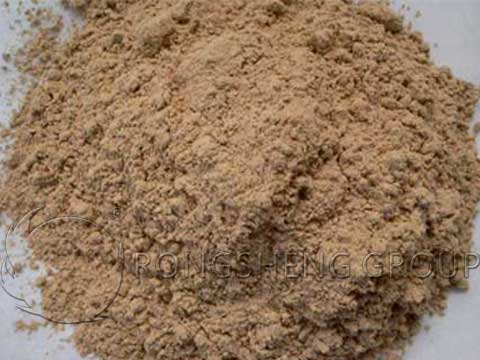
Refractory bricks require refractory mortar of the same material, and refractory mud is also prepared according to different grades of refractory bricks. For example, when building high alumina bricks and clay bricks, 5% high alumina fire clay and clay fire clay are prepared.
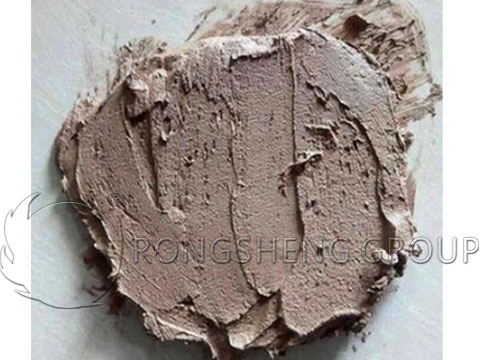
Modification of Refractory Mortar
General refractory mortar is prepared with water. The proportion of water added is between 25-30%, depending on the construction situation on site. If the temperature of refractory bricks for furnace lining exceeds 1350℃, high-grade refractory bricks are required. Then refractory mortar needs refractory mud with strong plasticity to fill the joints of refractory bricks and enhance the strength and life of the product.
What are the Disadvantages of Refractory Mortar Made with Water?
The disadvantage of refractory mortar prepared with water is that the strength and cohesiveness are not as good as refractory mortar prepared by phosphoric acid. The refractory mud prepared with water may drop bricks. The strength of the cold state is low, and the prepared refractory bricks cannot be integrated quickly. The setting time is not as good as that of refractory clay combined with phosphoric acid.
The refractory clay prepared by phosphoric acid has strong adhesion and strength. It can increase the strength with the refractory bricks of the masonry in the process of increasing the temperature. And when it is fused with refractory bricks, it will not fall off when it is bonded with refractory bricks.
The criterion for refractory mortar is the cold bonding strength between the fire mud and the masonry refractory brick, which has sufficient strength even when the service temperature exceeds 1350°C. There are many kinds of mixing agents for refractory mud, including binders such as water glass, phosphoric acid, and CMC. The refractory mortar prepared by the water glass solution produces silica gel, which is suitable for use with acid refractory bricks.
The refractory clay used for the lightweight refractory bricks is also the refractory clay of the same material, and the refractory clay used for the clay bricks and the lightweight clay bricks is the same. It also produces strength and adhesion. If it is a high-alumina brick with an aluminum content of more than 60%, high-alumina refractory clay should be used, and the refractory bricks of corundum products should be used with corundum-based fire clay.
The refractory mortar prepared by adding water does not have the refractory mud added with a water glass or phosphoric acid. It has a fast setting speed and does not become thick after storage for 12 hours. However, the storage time of refractory mortar prepared by water is not long, and there is the phenomenon of mud above water and below. The fire mud prepared by water glass or phosphoric acid aqueous solution has good fluidity and maximum bonding strength.
In short, no matter what kind of refractory mortar is used, it must be determined according to the refractory bricks and temperature used. Refractory mud prepared with water or refractory mud with other binders is also selected according to specific actual conditions.