The Importance of Refractory Solutions for CFB Cyclone Systems. Circulating Fluidized Bed (CFB) boilers are widely used in industries for energy production, thanks to their efficiency and ability to handle a variety of fuels. However, CFB systems, particularly the cyclone and connecting areas, operate under extreme conditions, including high temperatures, erosion, and chemical corrosion. To protect these critical components, the use of high-performance refractory materials is essential.
One such material is Low Cement Castable (LCC), a pouring-type refractory that offers enhanced strength, durability, and resistance to the harsh environments found in CFB systems. This blog will discuss how low cement castables are specifically designed for CFB cyclone systems and their connecting areas, and why they are the preferred solution for these demanding applications.
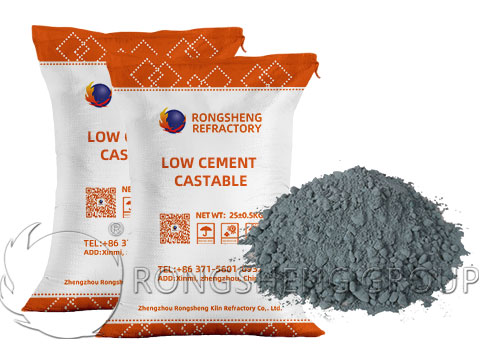
What is Low Cement Castable (Pouring Type)?
Definition and Composition
Low cement castable (LCC) is a type of refractory material that contains a lower percentage of cement, typically less than 3%. By reducing the cement content, these castables offer superior properties compared to traditional high-cement castables, such as enhanced mechanical strength, reduced porosity, and improved resistance to chemical attack. The pouring-type LCC is mixed with water and poured into forms or molds, making it easier to install in various shapes and configurations, including those in the cyclone and connecting areas of CFB boilers.
Key Properties of Low Cement Castable
- High mechanical strength: The reduced cement content increases the overall density of the material, providing greater mechanical strength and durability. This makes LCC ideal for high-stress areas in CFB systems.
- Abrasion resistance: In the CFB cyclone and connecting areas, refractory linings are subject to constant abrasive forces due to the flow of solid particles. Low cement castables are designed to resist erosion, prolonging the service life of the refractory lining.
- Thermal shock resistance: LCCs exhibit excellent resistance to thermal cycling, an essential property in CFB boilers, which operate under fluctuating temperatures.
- Chemical resistance: The aggressive chemical environment in CFB systems, particularly in the cyclone area, can lead to rapid degradation of refractory materials. Low cement castables have higher resistance to corrosion by acidic and alkaline compounds, ensuring long-term protection.
- Lower porosity: Reducing the cement content results in fewer pores, improving the material’s ability to resist the penetration of gases and slag. This feature is crucial for maintaining the structural integrity of the refractory lining.
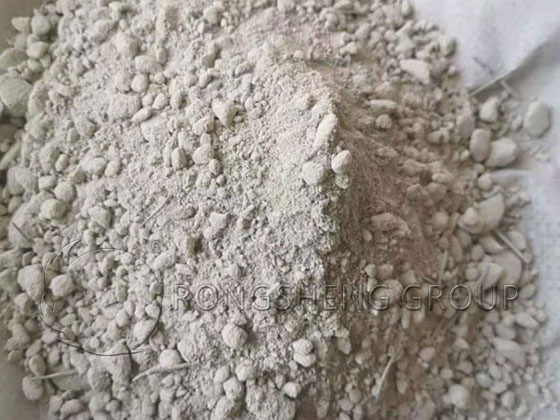
The Role of Low Cement Castables in CFB Cyclone Systems
Why the CFB Cyclone Needs High-Performance Refractories
The cyclone is a critical part of the CFB system, responsible for separating solids from gases. This area operates under high temperatures, often exceeding 900°C (1650°F), and experiences intense abrasion as particles are continuously circulated. The refractory material lining the cyclone must be able to withstand these conditions to prevent damage and ensure efficient operation.
Traditional refractory materials often fail prematurely in this environment due to thermal stress and mechanical wear. This is where low cement castables come into play, offering a solution that can handle the cyclone’s extreme demands.
Benefits of Using Low Cement Castables in CFB Cyclones
- Increased durability: The abrasion resistance of LCCs helps minimize wear caused by circulating solid particles, reducing the need for frequent maintenance.
- Enhanced energy efficiency: By providing better insulation and reducing heat loss, low cement castables help improve the overall efficiency of the CFB boiler.
- Improved operational reliability: Using high-quality LCCs in the cyclone ensures that the refractory lining remains intact for longer periods, reducing the likelihood of unplanned shutdowns due to refractory failure.
Low Cement Castables for the Connecting Area of CFB Systems
Challenges in the Connecting Area
The connecting area of a CFB boiler links different components, such as the cyclone and combustion chamber. This area is often subjected to a wide range of temperatures and mechanical forces, making it particularly vulnerable to wear and tear. The refractory material used here must be versatile, offering both high thermal resistance and the ability to endure mechanical strain.
Why Low Cement Castables are Ideal for the Connecting Area
- Flexibility in application: The pouring-type low cement castable can be easily applied in the connecting area, ensuring a seamless fit even in complex or irregular shapes.
- Thermal shock resistance: LCCs can handle rapid temperature changes, a common occurrence in the connecting area, without cracking or spalling.
- Resistance to chemical attack: The connecting area may also be exposed to aggressive chemical environments, particularly from flue gases. Low cement castables provide excellent resistance to these conditions, ensuring longer-lasting protection.

Installation and Maintenance Considerations for Low Cement Castables
Ease of Installation
One of the key advantages of low cement castables is their ease of installation. The pouring-type LCC can be mixed with water and poured into place, making it ideal for use in complex or hard-to-reach areas. This reduces installation time and ensures that the refractory lining conforms to the precise shape of the cyclone or connecting area, minimizing gaps and improving performance.
Maintenance and Longevity
Low cement castables offer extended service life due to their superior properties. However, regular maintenance is still essential to ensure optimal performance. Inspecting the lining for signs of wear and addressing any damage promptly can prevent costly repairs or unplanned downtime. When maintenance is required, LCCs are easy to repair, and their fast installation allows for quick turnarounds, minimizing disruption to operations.
The Superior Choice for CFB Cyclone and Connecting Areas
Low cement castables (pouring type) are an essential component in ensuring the reliability and efficiency of CFB cyclone systems and their connecting areas. Their superior mechanical strength, abrasion resistance, and thermal shock properties make them the ideal refractory material for these critical parts of the CFB boiler. By choosing high-quality LCCs, industries can reduce maintenance costs, improve operational efficiency, and extend the service life of their boilers.
RS Monolithic Refractory Manufacturer is committed to providing top-tier low cement castables specifically designed for CFB systems. Contact RS Manufacturer for prices. Our products offer the strength and durability needed to perform in the most demanding environments, ensuring your CFB boiler operates at peak efficiency for years to come.