The types of refractory castables for nickel-iron rotary kilns in Vietnam include high-alumina high-strength castables, corundum-mullite castables, and low-cement castables. As an experienced monolithic refractory manufacturer and sales manufacturer, the physical and chemical indicators of various castables of Rongsheng are customized according to the working environment conditions of high-temperature industrial kilns. The low-cement castables used in Vietnam’s nickel-iron rotary kiln have great advantages in their practical parts, which greatly improve the service life of the nickel-iron rotary kiln lining. The total amount of refractory materials used in the Vietnam nickel-iron rotary kiln project is about 1,200 tons, of which there are more than 500 tons of monolithic refractory castables and more than 600 tons of castable prefabricated parts. The masonry method of the rotary kiln has good practicability.
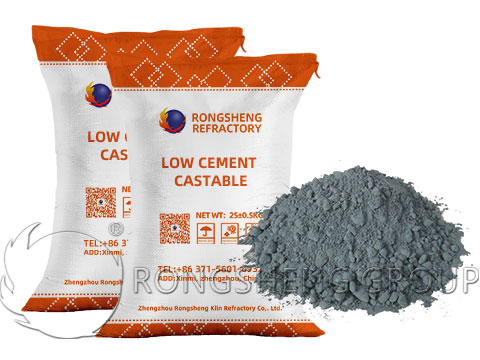
Low Cement Castables for Nickel-Iron Rotary Kiln
Low cement castables are also widely used in practical applications. It is mainly suitable for high-temperature linings such as rotary kilns, blast furnace tapholes, heating furnaces, shaft furnaces, heat treatment furnaces, calciners, tertiary air ducts, and preheaters. The service temperature of low-cement castable refractory is higher than that of ordinary refractory castables. However, when using it, a reasonable high-temperature curve should be formulated and explosion-proof fibers should be added to prevent bursting and falling off, so as to ensure the service life of low-cement castables. Thereby improving the overall use effect of the kiln.
Advantages of mixed masonry with monolithic castables and prefabricated parts in nickel-iron rotary kiln
- Stabilized the thermal system and improved the operation rate of the equipment. Compared with equipment of the same specification, the operating rate has increased by 10%. Yield is therefore also increased by 5%-10%. The processing capacity is strong, and the economic benefits created are higher.
- The relatively important calcination system of the nickel-iron rotary kiln adopts the advanced hydraulic stop wheel device at home and abroad through technological innovation and the metering plunger pump with high metering accuracy. Domestic advanced technologies such as high-precision speed regulating valves and contact graphite block sealing devices make the operation process scientific and reasonable. It guarantees the good quality of the kiln products.
- The finished product of the nickel-iron rotary kiln is high, and the output of the kiln is high. On the other hand, it is also conducive to laying the foundation for further fine processing of downstream users or ferronickel. Technology is more mature and technology is more conducive to development.

Low Cement Refractory Castable for Rotary Kiln
Low-cement refractory castables mainly include high-alumina, mullite, and corundum refractory castables. This series of products has the characteristics of high strength, erosion resistance, wear resistance, and excellent performance. At the same time, the material can be made into a quick-baking explosion-proof castable according to the user’s baking time requirements.
Construction of High Aluminum Low Cement Castable for Rotary Kiln Lining
The construction of high-alumina low-cement castables for rotary kiln lining requires attention to the retention of expansion joints, control of construction temperature, mixing, construction, and maintenance.
- Retention of expansion joints
According to previous experience using high-alumina low-cement castables, the expansion joint is a key factor affecting the service life of the rotary kiln castable lining. The expansion joint of the rotary kiln lining is determined as follows:
- (1) Ring seam. For a section of 5m, the method of clamping 20mm alumina silicate fiber felt is used between the surrounding casting body. After expansion, the fibers are compacted to buffer the expansion stress.
- (2) Flat seams. Every three pieces of cast body clamp five-plywood with a depth of 100mm in the direction of the inner circumference. There are 6 seams at the working end.
- (3) 25 exhaust plugs are used per square meter during pouring. While the kiln is exhausted, a certain amount of expansion stress is released.
- Determination and control of construction temperature
The suitable construction temperature for high-alumina low-cement castable refractory is 10-30°C. If the ambient temperature is low, take the following measures. (1) Close the surrounding construction environment, increase heating facilities, and strictly prevent freezing. (2) Use hot water to mix the ingredients. Generally, hot water at 35-50°C is used, and the specific conditions need to be determined according to the conditions of the on-site pouring vibration test.
- Mixing
First of all, it is necessary to determine the amount of stirring at one time according to the capacity of the mixer. After the mixing amount is determined, add the pouring material in the packaging bag and the small package additive in the bag to the mixer at the same time. First start the mixer and dry mix for 2~3min. Then add the water weighed in advance to 4/5, and stir for 2~3min. Next, determine whether to add the remaining 1/5 of water according to the viscosity of the mixing material. If water needs to be added, it needs to be fully mixed before trial pouring. Determine the amount of water to be added in combination with the situation of vibrating slurry. After the amount of water added is determined, it must be strictly controlled. In the case of ensuring that the vibrating slurry can be turned, water should be added as little as possible (add water strictly according to the instructions of the manufacturer).
- Construction
The construction time of the high-alumina low-cement castable is about 30 minutes. The dehydrated or coagulated materials cannot be mixed with water and should be resolutely discarded. The vibrating rod is used to vibrate to achieve pulping and compaction. The vibrating rod should have a backup so that the spare rod can be activated when the vibrating rod breaks down.
The construction of castables should be carried out in strips along the axis of the rotary kiln, and the construction surface should be cleaned before pouring each strip. There must be no dust, welding slag, or other sundries. At the same time, check whether the welding of the anchors and the asphalt paint treatment on the surface are in place. Otherwise, remedial measures should be taken.
In the strip construction, the construction of the strip casting body should first be open-poured in the lower part of the kiln body from the kiln tail to the kiln head. The support of the formwork shall be carried out between the anchor and the steel plate. The steel plate and the anchors are inlaid firmly with wooden blocks. The height of the formwork is 220mm, the width is 620mm, the length is 4-5m, and the central angle is 22.5°.
The construction of the second pouring body should be carried out after the pouring strip is finally set and the formwork is removed. On one side, the method of supporting arc-shaped formwork is used to seal the pouring from the kiln head to the kiln tail. And so on…
When the castable is vibrating, the mixed mud should be added to the tire mold while vibrating. The control of the vibration time should be based on the fact that there are no obvious bubbles coming out of the grout on the surface of the cast body. The de-moulding time should be determined by the ambient temperature of the construction site, and the de-moulding should be ensured after the castable has finally been set and has a certain strength.
- Baking of the lining
How to bake low cement castable refractory for the rotary kiln? The rotary kiln uses shaped refractory bricks as the lining material. Because the refractory bricks are high-temperature sintered products and do not contain moisture, the purpose of the kiln is to bake the joint materials of the refractory bricks. In order to achieve a close combination between the bricks, therefore, the kiln lining built with refractory bricks has a short drying time. When using amorphous refractory castables as the inner lining, it is made by mixing bulk materials with water, and the castables have not been fully pre-fired. The structure is unstable at low temperatures, and the water content is relatively large. If the kiln is too fast, the inner lining will crack due to the rapid discharge of water. Therefore, the drying time of the kiln should be extended appropriately according to the unused situation.
Rongsheng Monolithic Refractory Castable Manufacturer
Design and construction of monolithic refractory castables, design, construction, and solutions of high-temperature industrial kiln refractory lining and insulation layer lining. Rongsheng sells low cement refractory castable for ferronickel rotary kilns, lc 70 castable, contact us for free samples and quotations.