Refractory ramming materials are classified into clay ramming materials, high alumina ramming materials, carbon ramming materials, magnesia ramming materials, and dolomite ramming materials. The construction methods are also different. The following describes the construction methods of three different types of ramming materials commonly used.
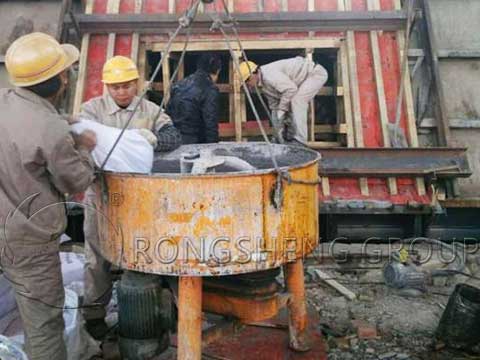
Construction of High Alumina (Clay) Ramming Material
- (1) Stirring. First, add the coarse and fine aggregates and the binder (high alumina cement) in the prescribed proportions to the forced mixer for dry mixing for 1 to 2 minutes. Next, add a certain amount of water and mix and stir for about 5 minutes.
- (2) Construction. The thickness of the mixed ramming material is 80-100mm at one time. A pneumatic hammer is used to ram continuously and evenly until the number of reciprocations of the specified bulk density is reached.
Construction of Carbon Ramming Material
The carbon ramming material can be constructed by the cold ramming method or the hot ramming method. At present, the commonly used and convenient construction is the cold ramming method.
Regardless of the carbon material used for the construction method, the finished material should be used. Cold ramming carbon material can generally be put into use directly. Before ramming the hot ramming carbon material, the carbon material must be crushed in advance. And conduct uniform heating, and the heating temperature depends on the mixing temperature of the finished material. There should be no hard lumps in the heated carbon material. When ramming, the hammerhead should be heated to dark brown, and the material temperature should not be lower than 70℃.
Before the carbon material is rammed, the working surface should be cleaned, and then the carbon material should be poured in the layer by layer, and the thickness of each layer should not exceed 100mm. A pneumatic hammer is used to ramming several times with one hammer and half hammer. The density of each layer of ramming should be checked according to the specified density or compression ratio, and the compression ratio should be 40%-45%.
Before ramming the next layer of carbon material, the rammed surface should be roughened to facilitate the tight bonding of the upper and lower layers.
Construction of Magnesia Ramming Material
Magnesium ramming materials have different binders, including tar magnesia and brine magnesia. It is mostly used at the bottom of converters, electric furnaces, copper reverberatory furnaces, and flash furnaces.
Before the construction of the tar magnesia ramming material, the coal tar should be heated to about 130°C for dehydration, and the magnesia and iron oxide powder should be heated to above 110°C for drying.
After the bricklaying is completed, heat and dry the surface of the wet brickwork. In order to remove the water (dry masonry does not need to be heated), and paint a layer of coal tar on the surface of the masonry.
When ramming, pour the mixed ramming material into layers. The thickness of each layer is 70-80mm, and the compression ratio is 50%. Ramming is usually carried out from the center of the furnace to the surroundings to prevent the oil from squeezing toward the center to form a soft spot (spring body). The wind pressure for ramming should not be less than 0.5MPa.
The ramming method of brine magnesia ramming material is similar to that of tar magnesia ramming.
For more information about refractory ramming materials and the construction methods and precautions of refractory ramming materials, please contact us. Not only can we provide high-quality refractory products, but we also have comprehensive customer service.